In the world of construction, choosing the right materials can make all the difference. Did you know precast and prefabricated concrete are not the same? Our blog will clear up any confusion, detailing each process’s distinct methods and benefits.
Key Takeaways
- Precast concrete is poured and cured in controlled factory settings, creating standardized shapes that are then transported to the construction site for assembly.
- Prefabricated construction involves assembling pre-made building components on-site, allowing for more customization and flexibility in design compared to precast methods.
- Precast offers high – quality control and faster construction due to mass production, while prefabricated provides the opportunity for greater design variety and onsite adjustments.
- Challenges faced by both methods include transportation logistics and the need for careful installation to maintain structural integrity throughout the construction process.
- When choosing between precast or prefabricated concrete, factors like project specifications, environmental impact goals, cost-effectiveness, and resource allocation should be thoroughly evaluated.
Understanding Precast and Prefabricated Construction
Precast construction involves casting concrete in a reusable mold or form at the factory and then transporting it to the construction site for assembly. On the other hand, prefabricated construction refers to assembling building components off-site and then transporting them to the construction site for installation.
Definition of precast construction
Precast construction transforms concrete into a multitude of shapes and sizes by pouring it into reusable molds. These molds are crafted to create different building components, often in a factory setting where conditions like temperature and humidity are strictly controlled.
Once the concrete hardens, these pre-formed units are then transported to the construction site ready for installation.
The process streamlines building projects because it allows for simultaneous progress on-site preparation work and component manufacturing. It also makes way for high-quality control standards due to the standardized nature of production in an industrial environment.
By using this method, builders benefit from reduced waste, resource efficiency, faster construction times, and ultimately lower overall carbon emissions—a significant advancement over more traditional construction techniques.
Definition of prefabricated construction
After understanding precast construction, it’s crucial to delve into the definition of prefabricated construction. Prefabricated construction involves assembling pre-made components at the construction site rather than pouring concrete into molds at a factory.
This method allows for more changes and customization during the assembly process, accommodating specific project requirements. The tight production control in prefabricated construction guarantees safety, quality, and durability, ensuring that structures meet stringent standards.
Components can be produced in various settings, offering flexibility while maintaining precision and efficiency.
Prefabricated construction involves on-site assembly of pre-made components rather than casting concrete in molds at a factory environment. This method provides greater flexibility and customization opportunities to cater to unique project needs.
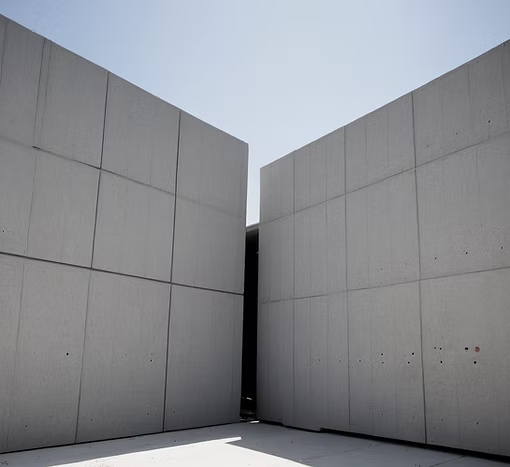
Key Differences Between Precast and Prefabricated Concrete
The construction process for precast concrete involves pouring and setting the concrete in a controlled environment, while prefabricated construction involves assembling standardized components on site.
Additionally, precast concrete allows for more customization, whereas prefabricated construction offers efficiency in manufacturing and assembly.
Construction process
Precast concrete involves pouring the material into molds at a factory and letting it cure before transport to the construction site. Once on-site, these pre-made components are assembled like building blocks, which offers faster erection and reduced labor costs.
On the other hand, prefabricated construction assembles pre-made components directly at the construction site, allowing for greater design flexibility and customization. This method typically involves materials beyond just concrete, but also steel and wood, providing a more diverse range of building options.
As we delve deeper into understanding how precast and prefabricated methods differ in terms of modular construction processes and industrial use, let’s explore their distinct advantages seen in quality control measures.
Customizability
Precast concrete structures are typically more standardized and mass-produced, limiting the level of customization available. In contrast, prefabricated construction allows for greater flexibility and adaptability in design, making it well-suited to meet specific project requirements.
This enhanced customizability enables architects and engineers to tailor the components to the unique needs of each construction project, offering a wide range of architectural possibilities while ensuring structural integrity.
Prefabricated concrete structures can be customized according to size, shape, color, finishes, and other specifications. This versatility provides builders with the freedom to create innovative designs that align with their vision while meeting functional requirements.
Location of manufacture
While customizability focuses on design flexibility, the location of manufacture plays a crucial role in the construction process. Precast concrete components are predominantly manufactured in specialized factories with controlled conditions.
This results in tight production control, ensuring high standards of safety, quality, and durability. On the other hand, prefabricated components can be produced in a variety of settings, offering more flexibility but potentially leading to variations in production control.
Both precast and prefabricated methods offer efficient processes for manufacturing concrete components – with precast focusing on producing standardized products within controlled environments and prefabricated construction allowing for more versatility but potential fluctuations in production standards.
Benefits and Challenges of Using Precast and Prefabricated Concrete
Using precast concrete offers advantages such as faster construction times, high quality control, and durability. However, challenges include transportation costs and limited customization options.
Prefabricated construction can save time and money, but may face issues with design flexibility and site access.
Advantages of precast concrete
Precast concrete offers improved precision and quality due to the controlled conditions in which it is manufactured. This method provides significant benefits including:
- Increased durability and strength of structures
- Reduction in construction time and labor costs
- Lower carbon emissions and better resource allocation
- High level of standardization and mass – production, leading to cost savings
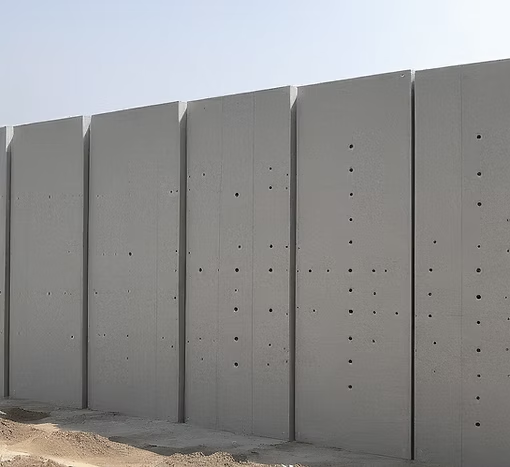
Advantages of prefabricated construction
When comparing with precast concrete, prefabricated construction offers several advantages:
- Allows for greater design flexibility and customization, enabling architects and engineers to create unique and tailored structures for specific project requirements.
- Provides better quality control and assurance of safety due to the controlled environment in which components are manufactured, resulting in higher precision and consistency in construction.
- Enables faster construction times by allowing simultaneous on-site preparation while off-site manufacturing takes place, reducing overall project duration.
- Offers potential cost savings through reduced labor requirements, streamlined construction processes, and minimized material waste during assembly.
- Enhances sustainability by optimizing resource allocation, minimizing environmental impact through reduced energy consumption and waste production, contributing to lower carbon emissions.
Challenges of precast and prefabricated construction
- Transportation can be a challenge for precast concrete components due to their size and weight, requiring careful planning and logistics during delivery to the construction site.
- Proper handling and installation of precast and prefabricated components is crucial to ensuring structural integrity and minimizing the risk of damage during transit and assembly.
- Weather conditions can impact the production and delivery schedules of precast and prefabricated components, resulting in potential delays if not adequately accounted for in project planning.
- Coordination between various trades and contractors is essential for successful integration of precast and prefabricated elements into the overall construction process, requiring meticulous communication and scheduling efforts.
- Quality control throughout the manufacturing, transportation, and installation phases is imperative to address any defects or discrepancies in precast or prefabricated components, ensuring compliance with safety standards and project specifications.
Considerations before choosing a method
When deciding between precast and prefabricated concrete methods, it’s crucial to consider project requirements, customization needs, and production control. Evaluating the level of design flexibility required and the specific environmental impact goals can help in making an informed decision.
Additionally, factoring in factors such as waste management, resource allocation, and overall construction timeline can further guide the choice between precast and prefabricated concrete methods.
Finally, assessing transportation logistics for delivering components to the construction site is essential in ensuring efficient project execution.
Concluding Thoughts
Both precast and prefabricated concrete construction methods offer various benefits and challenges. They both contribute to faster construction times, reduced waste, lower carbon emissions, and cost savings compared to traditional cast-in-place methods.
However, the choice between precast and prefabricated concrete ultimately depends on project requirements such as design flexibility, customization needs, safety guarantees, production control, and resource allocation considerations.
The decision-making process should involve careful consideration of the specific advantages each method offers in terms of efficiency, quality control, environmental impact, cost-effectiveness, and functionality within the context of the construction project’s unique demands.
This thoughtful approach ensures that the chosen method aligns with the overall goals and objectives of the construction project while optimizing its long-term outcomes.
Conclusion
In conclusion, understanding the differences between precast and prefabricated concrete is crucial for informed decision-making in construction. Precast construction involves pouring concrete into reusable molds, while prefabricated construction assembles pre-made components at the site.
The choice between these methods can impact design flexibility, production control, and environmental considerations. Considerations before choosing a method include project needs, customization requirements, and sustainability goals within the construction industry.
FAQs
1. What are precast and prefabricated concrete?
Precast concrete is a type of building material that’s formed in molds off-site, then transported to the construction location. Prefabricated concrete also involves creating components off-site, but it can include a variety of materials combined with concrete.
2. How does precast concrete benefit the construction industry?
Precast concrete speeds up construction times because it’s made ahead of time in a controlled environment which ensures consistent quality and structural engineering standards are met before being used at the building site.
3. In what ways do both precast and prefabricated structures support building technology?
Both types use modern building technology to create strong, durable parts for buildings or other structures that save time during assembly on-site compared to traditional methods.
4. Can you tell me one main difference between precast and prefab concrete products?
The main difference is that all precast products are solely made out of concrete, while prefabricated units may combine different construction materials into panels or modules ready for quick installation.
Recent Posts
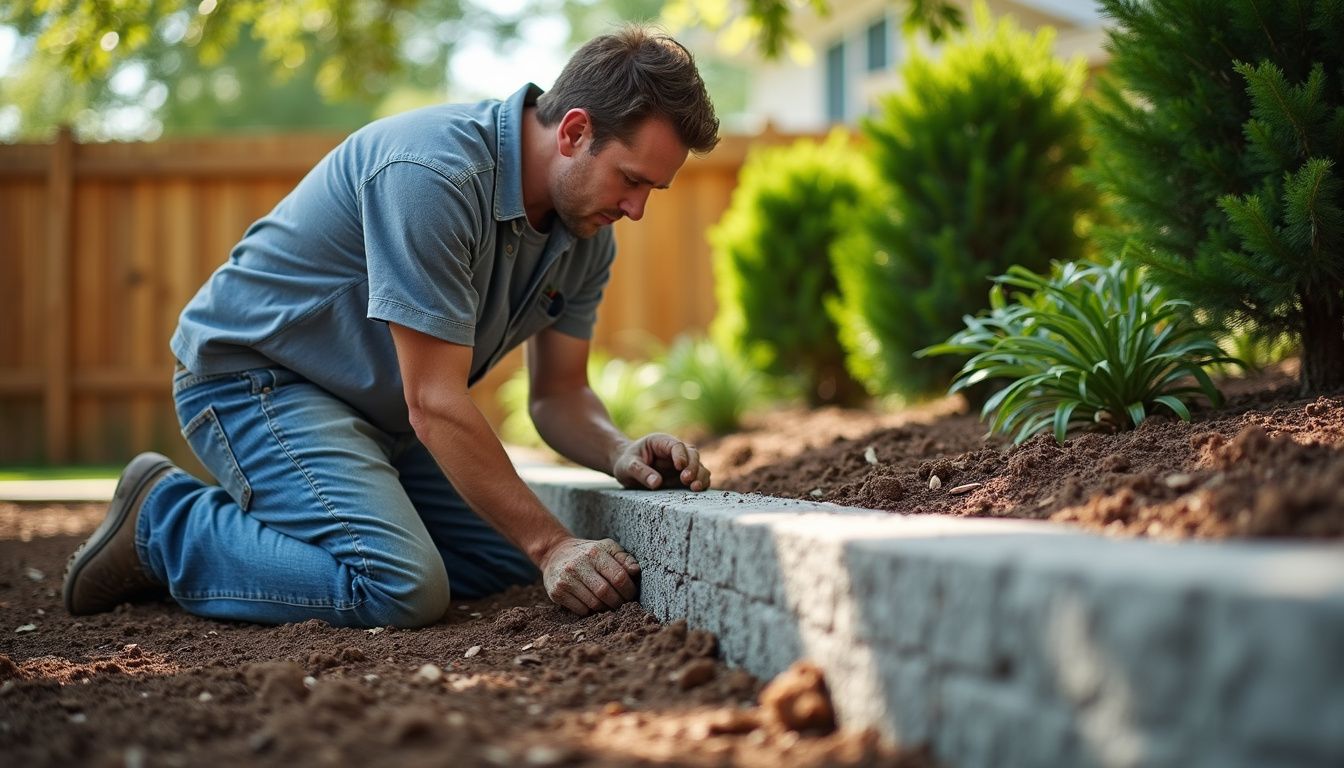
Why Landscaping Pros Prefer Precast Concrete Over Poured-in-Place
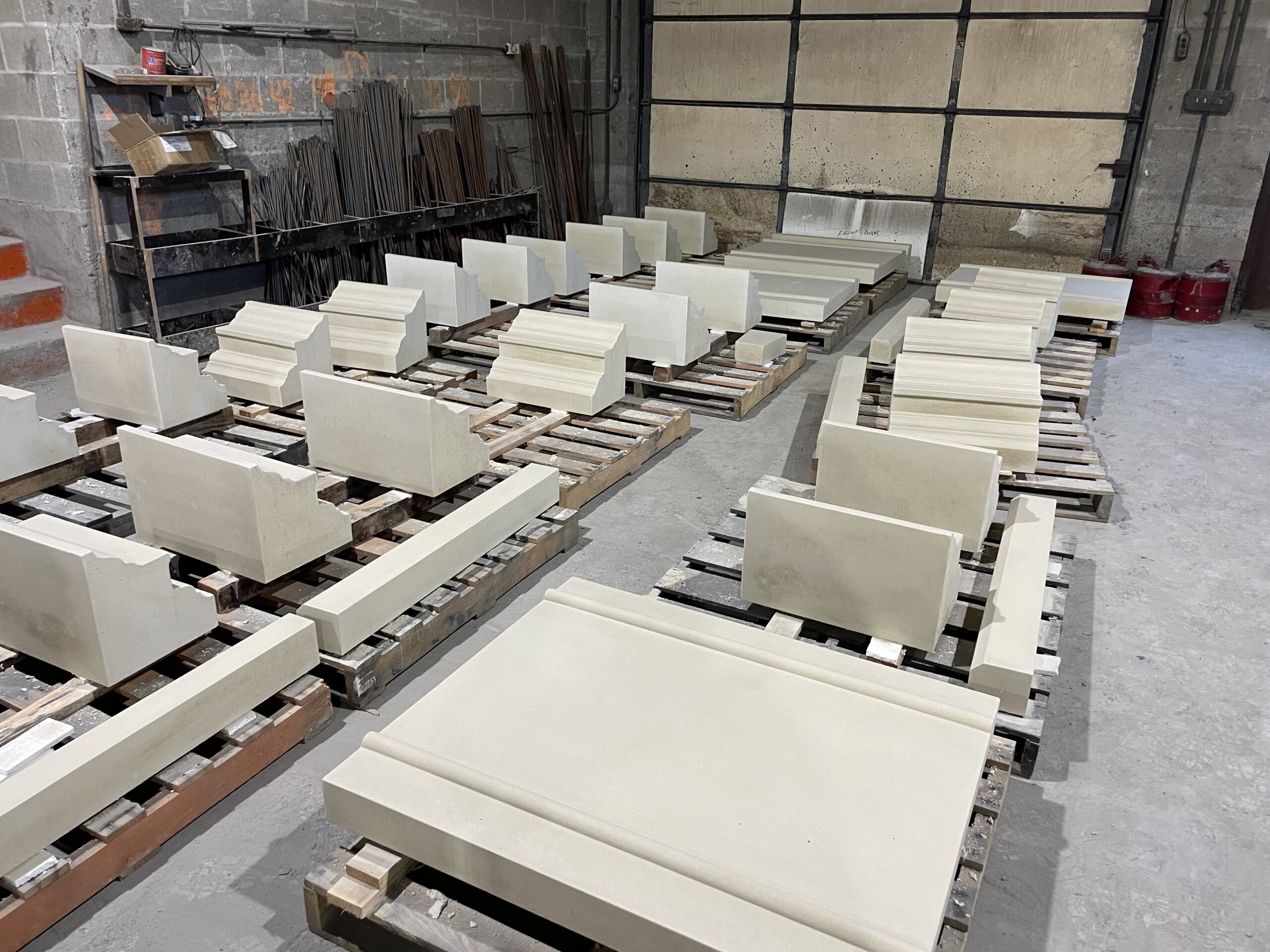
Why & How is Precast Concrete Prestressed?
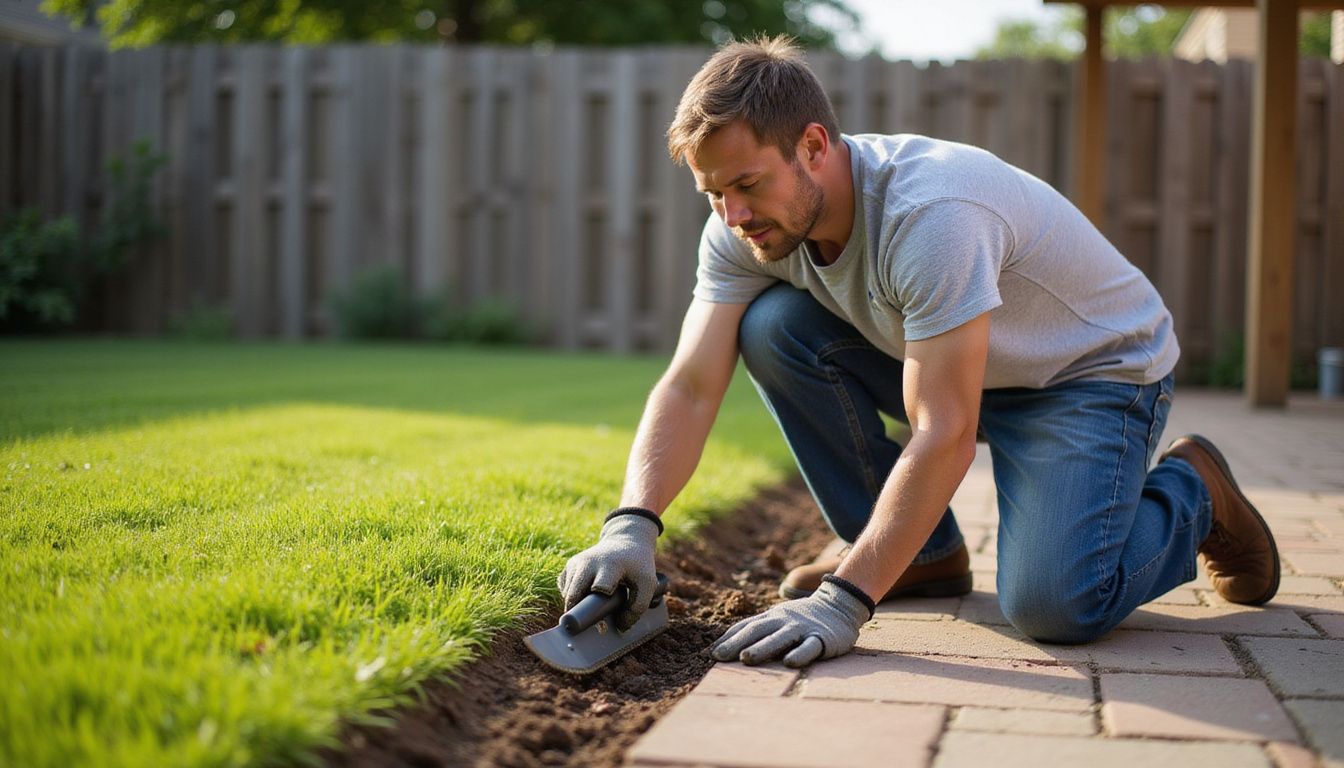