When planning to build or renovate, choosing the right floor panels is crucial. Hollow core precast concrete floor panels are popular for their strength and ease of installation. Yet, they come with challenges that can affect your project timeline and budget.
Key Takeaways
- Hollow core precast concrete floor panels demand a significant upfront investment, which includes the costs of machinery, equipment for installation, and coordination with specialist sub-contractors.
- These panels pose difficulties when it comes to repairs and reinforcements due to their design; accessing the hollow cores for maintenance or modifications can be complex and costly.
- Transporting and installing these heavy slabs requires careful planning as well as specialized lifting equipment and vehicles; improper handling can lead to damage or misalignment that impacts construction integrity.
- Design flexibility is limited with hollow core precast concrete floor panels; their prefabricated nature means they can’t be easily adjusted on-site to meet specific architectural demands or styles.
- Considering alternatives like solid slabs, slabs without beams, or ribbed slabs might better align with project requirements in terms of design versatility, ease of installation, and cost-effectiveness.
Understanding Hollow Core Precast Concrete Floor Panels
Hollow core precast concrete floor panels are prefabricated slabs used in construction for their lightweight and structural integrity. They offer advantages such as quick installation, fire resistance, and sound insulation.
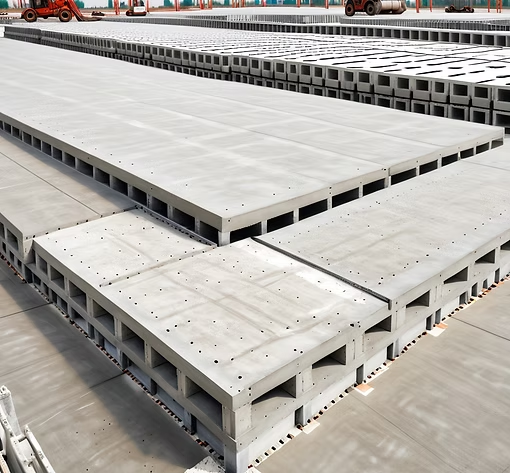
Definition and purpose
Hollow core precast concrete floor panels are innovative building materials designed for strength and efficiency. They consist of long, sturdy slabs with hollow tunnels running their length, which reduce weight and provide space for utilities.
These panels serve as a part of the structure’s flooring system, ideally suited to support heavy loads over wide spans without additional support columns. Their lightweight nature makes them easier to handle than solid reinforced concrete slabs while still retaining robust structural integrity.
The purpose of these precast slabs extends beyond simple support; they streamline the construction process by being made in controlled environments before arriving on-site ready to install.
This method speeds up building timelines and ensures consistent quality across projects. With their built-in insulation properties, hollow core panels also contribute towards energy efficiency in buildings by helping maintain stable indoor temperatures.
Advantages of using hollow core precast concrete floor panels
Using hollow core precast concrete floor panels offers several advantages, such as:
- Speed of Installation: Hollow core slabs allow for quick installation due to their prefabricated nature, saving time and labor costs.
- Durability: Precast concrete provides long-term durability, with minimal maintenance required over its lifespan.
- Energy Efficiency: The design and construction of hollow core slabs contribute to energy efficiency within buildings, reducing operational costs.
- Long Spans: These panels can cover large distances without the need for additional supporting structures, providing an open and flexible interior space.
- Fire Resistance: Hollow core precast concrete panels offer excellent fire resistance, enhancing the safety and security of the building.
- Sound Insulation: The solid nature of these floor panels provides effective sound insulation between floors, creating a quieter and more comfortable indoor environment.
Disadvantages of Hollow Core Precast Concrete Floor Panels
High initial investment, coordination with specialist sub-contractors, difficult repairs and strengthening, transportation and installation challenges, limited design flexibility.
High initial investment
Investing in hollow core precast concrete floor panels requires a substantial upfront financial commitment. The cost of the heavy precast concrete machinery and specialized equipment for lifting precast concrete adds to the initial investment.
Building with hollow core slabs demands careful consideration due to the high costs associated with setting up a precast concrete plant and coordinating with specialist sub-contractors on-site, which can impact project budgets significantly.
The use of hollow core slabs involves financial commitments from planning through installation, including costs for transportation and specialized equipment. This initial investment should be carefully weighed against the long-term benefits while considering alternatives such as solid slabs or ribbed slabs that may offer more cost-effective solutions.
Requires coordination with specialist sub-contractors
Coordinating with specialized sub-contractors is essential when installing hollow core precast concrete floor panels. Specialist knowledge and equipment are necessary to ensure the safe and accurate installation of these large, heavy components.
This coordination helps to prevent potential issues during the installation process, contributing to the overall success of the project.
Efficient coordination with specialist sub-contractors on-site ensures that the unique requirements of working with hollow core slabs are met. Specialized attention during installation can help address challenges specific to handling and placing these precast concrete elements, ultimately leading to a successful and durable flooring system.
Difficult to repair and strengthen
Repairing and strengthening hollow core precast concrete floor panels can be challenging due to their unique construction. Specialized equipment and techniques are often required to address any damage or deterioration.
Additionally, the hollow cores within the panels make it difficult to access and reinforce them effectively when needed. These challenges can result in increased maintenance costs and extended downtime for repairs, impacting the overall efficiency of the structure.
Furthermore, reinforcing or repairing hollow core slabs may necessitate specialized expertise, adding an extra layer of complexity to these tasks. The need for coordination with specialist sub-contractors for repair and reinforcement further emphasizes the intricate nature of working with hollow core precast concrete floor panels.
Transportation and installation challenges
Transporting and installing hollow core precast concrete floor panels present several challenges that need to be carefully considered:
- Size and weight: Hollow core slabs are large and heavy, requiring specialized equipment for lifting and transportation, considering their weight.
- Site access: Access to the construction site must be carefully planned due to the size of the panels, requiring coordination with transport logistics.
- Crane availability: To lift and position the heavy panels, cranes with sufficient capacity must be available for installation onsite.
- Handling requirements: The delicate nature of hollow core slabs demands careful handling during transportation and installation to avoid damage or breakage.
- Installation precision: Proper alignment during installation is crucial as any misalignment can impact the structural integrity of the entire floor system.
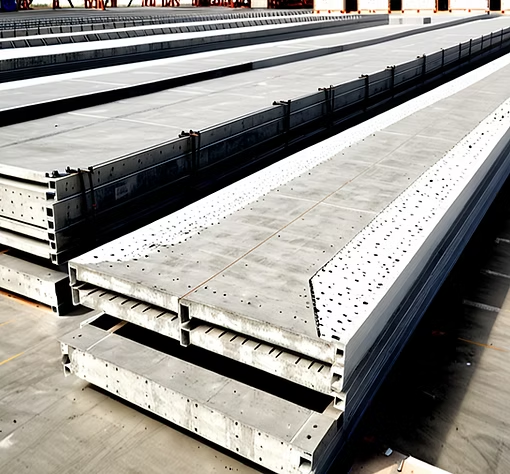
Limited design flexibility
Hollow core precast concrete floor panels offer limited design flexibility, making it challenging to achieve certain architectural features. The prefabricated nature of these panels restricts the ability to modify or customize them according to specific project requirements.
This limitation can impact the aesthetic appeal and functionality of the building, requiring careful consideration when opting for hollow core slabs.
When exploring alternatives to hollow core precast concrete floor panels, it’s essential to consider solutions that offer greater design adaptability while maintaining structural integrity.
Solid slab, slab without beams, and ribbed slab are viable options worth examining.
Alternatives to Hollow Core Precast Concrete Floor Panels
Consider alternatives such as solid slabs, slabs without beams, and ribbed slabs for your construction projects. Each alternative offers its own unique benefits and may better suit your specific project needs.
Solid slab
Solid slabs are a popular alternative to hollow core precast concrete floor panels. They offer enhanced structural strength and stability, making them suitable for heavy loads and high-traffic areas.
Unlike hollow core slabs, solid slabs provide superior resistance to impact and vibrations, reducing the need for frequent repairs and maintenance. With their simpler design, solid slabs also offer easier installation compared to hollow core panels.
Solid slab construction involves pouring concrete directly onto the formwork at the construction site, allowing for greater customization in terms of thickness and reinforcement. This flexibility makes them an attractive option for projects with specific load-bearing requirements or architectural constraints.
Slab without beams
Slab without beams offers a simpler structural form, reducing the complexity of installation and enhancing construction efficiency. This type of floor panel eliminates the need for additional beams, allowing for easier handling during transportation and installation on-site.
The absence of beams also provides more design flexibility and greater open space within the building, making it an attractive alternative to hollow core precast concrete floor panels.
Constructed in one solid piece, Slab without beams offers a seamless surface that contributes to its durability and stability, providing a reliable option for various construction projects.
Ribbed slab
Ribbed slabs are a type of precast concrete floor panels that feature a series of ribs running in one direction, providing increased strength and rigidity. These ribs also reduce the overall weight of the slab while maintaining structural integrity and load-bearing capacity.
The construction process for ribbed slabs involves using prefabricated molds to create the ribbed profile, resulting in efficient production and installation. Ribbed slabs offer advantages such as enhanced spans, reduced material usage, and improved acoustic performance compared to solid slabs or other types of precast concrete floor panels.
The design flexibility and cost-effectiveness of ribbed slabs make them a popular choice for buildings requiring long spans with minimal support points. Additionally, their ability to accommodate services within the floor depth enhances their suitability for various architectural and structural demands.
Conclusion
In conclusion, it’s important to weigh the advantages of hollow core precast concrete floor panels against their disadvantages before making a decision. Coordination with specialist sub-contractors and challenges in repair should be carefully considered.
The high initial investment and limited design flexibility are also significant drawbacks to bear in mind when evaluating this construction material option. Alternatives like solid slabs or slabs without beams may offer better solutions for some construction projects.
FAQs
1. What can go wrong with hollow core precast concrete floor panels?
Hollow core precast concrete floor panels might need repairs over time, and fixing them can be tricky because of their unique hollowcore slab details.
2. Is it hard to handle and move hollow core slabs?
Yes, special equipment for lifting is often needed to move large and heavy precast concrete pieces like hollow core slabs safely.
3. Can you tell me a downside of precast concrete used in retaining walls?
One disadvantage of using precast concrete for retaining walls is that they may not fit perfectly with the existing terrain, which could affect the wall’s stability and appearance.
4. Are there any specific weaknesses in concrete technology when it comes to hollowcore slabs?
While there are many advantages to using concrete technology for creating hollowcore slabs, one notable drawback is that if not made or installed correctly, they can be less durable than other types of flooring.
Recent Posts
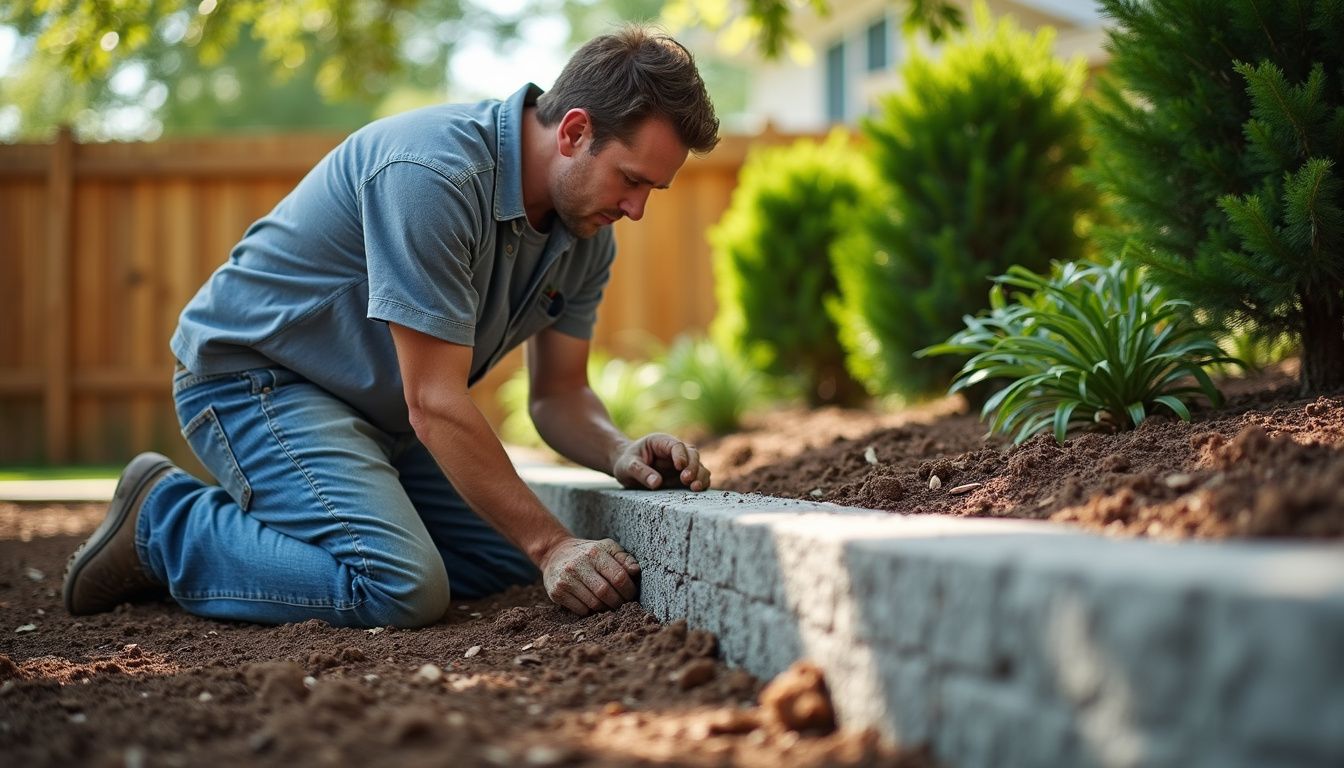
Why Landscaping Pros Prefer Precast Concrete Over Poured-in-Place
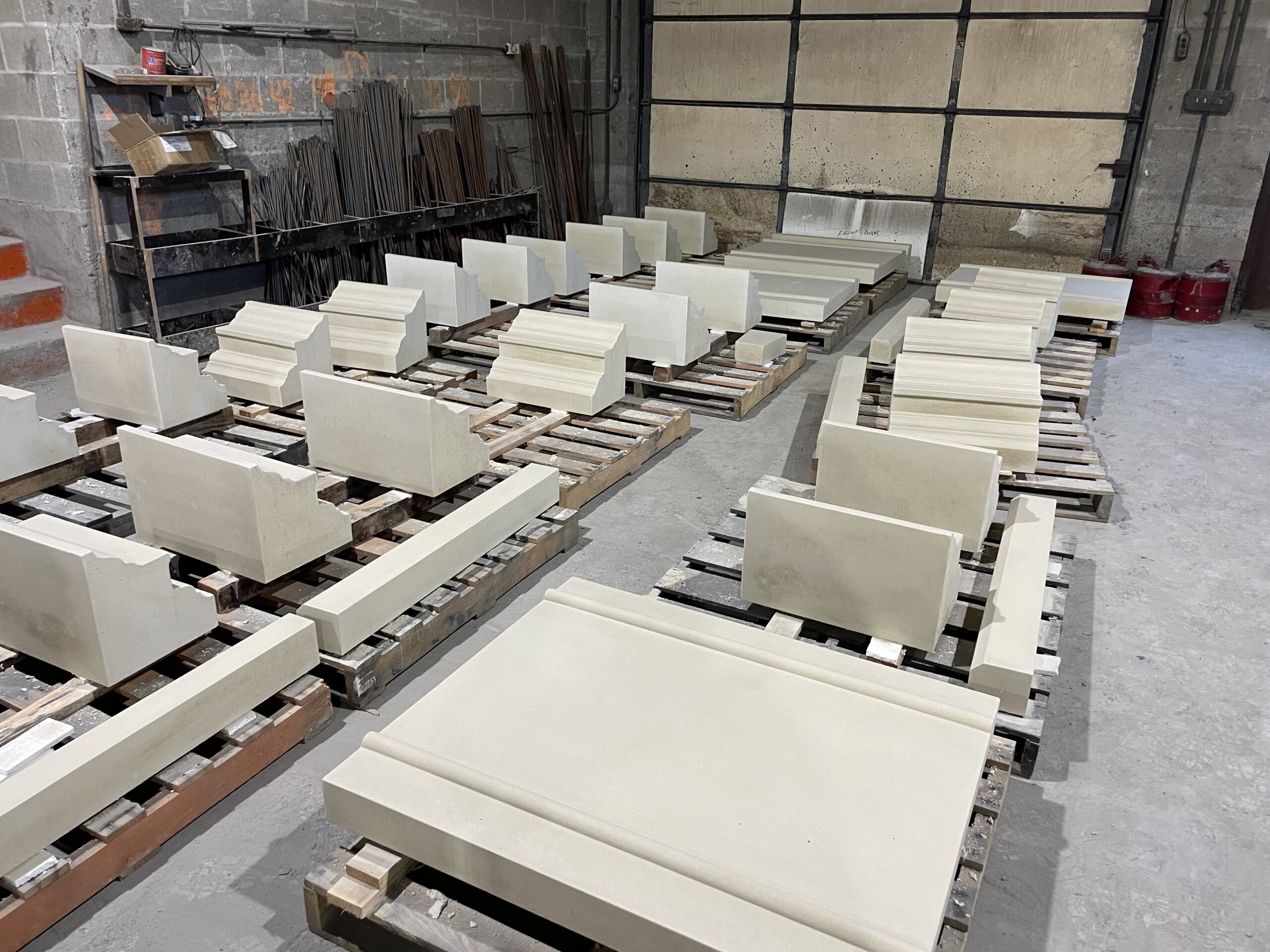
Why & How is Precast Concrete Prestressed?
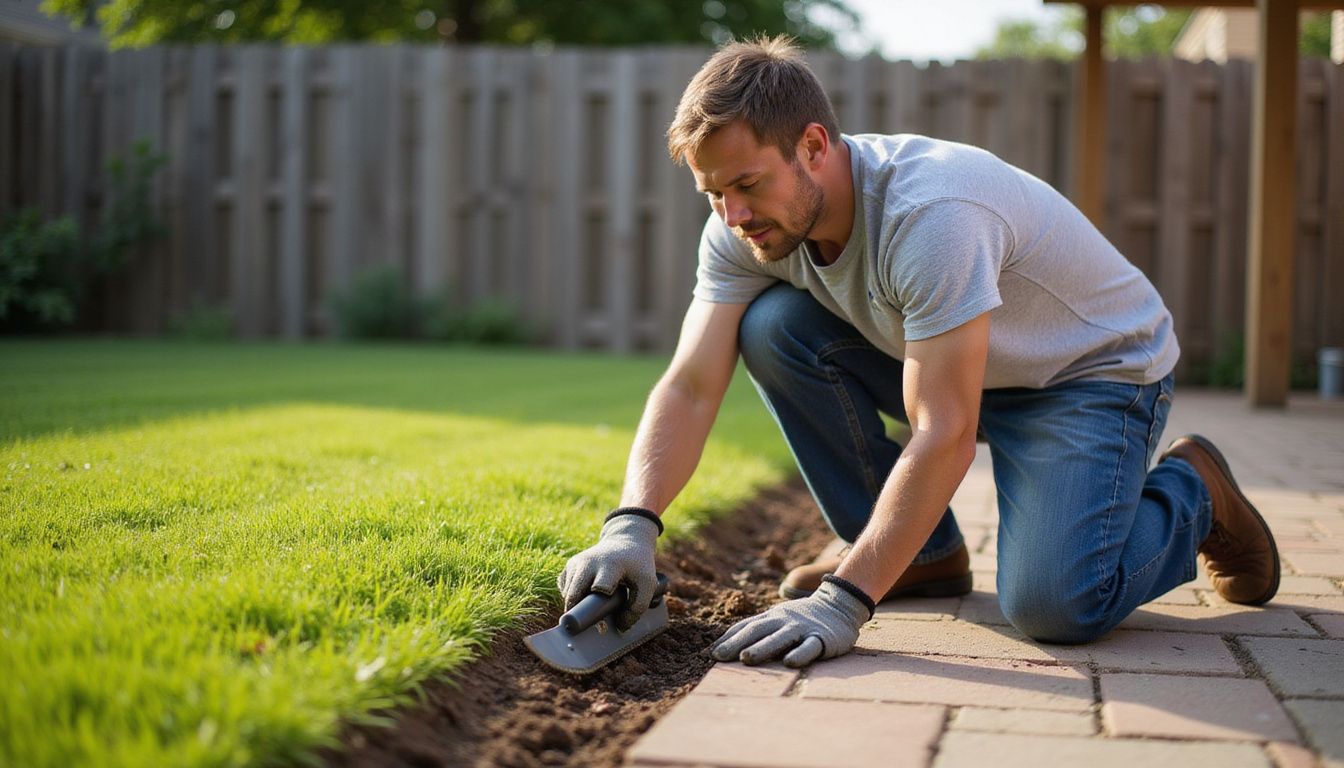