Building a warehouse can be a massive undertaking, often involving tight schedules and budget concerns. One notable fact is precast concrete’s reputation for quality assurance in construction due to its strength and resilience.
This article will guide you through the benefits of choosing precast concrete for your next warehouse project, offering time-saving and cost-effective solutions without compromising on quality.
Key Takeaways
- Precast concrete is a quick and cheap way to build strong warehouses.
- Warehouses built with precast concrete last a long time and don’t need much fixing up.
Benefits of Using Precast Concrete for Warehouse Construction
Using precast concrete for warehouse construction offers numerous benefits, including time and cost efficiency, structural strength and durability, design flexibility and aesthetic appeal, as well as improved lighting and safety.
Time and Cost Efficiency
Precast concrete speeds up warehouse building projects. Instead of waiting for concrete to set on-site, factories make precast pieces ahead of time. This means workers can put a warehouse together much faster. Faster construction saves money too, because it cuts down on labor costs and lets businesses use their warehouses sooner.
Warehouses built with precast concrete save cash over time as well. The strong materials last longer and need less fixing up. Their high quality means avoiding extra spending on repairs or replacements later on.
Precast concrete is smart for both saving time now and money later.
Structural Strength and Durability
Buildings made with precast concrete are very strong and can last a long time. This kind of construction is great for warehouses that need to hold a lot of weight, like heavy machinery or lots of products.
The walls, floors, beams, and columns all work together to make sure the building stays up and safe for many years. Precast concrete is tough against damage from things like forklifts or cars hitting it.
Design Flexibility and Aesthetic Appeal
Precast concrete isn’t just strong; it also gives builders the ability to customize the look of their warehouse. They can choose different shapes, colors, and textures to create a unique style for each building. There’s optionality to make the warehouse blend with its surroundings or stand out. This control makes sure every piece looks right and matches the designer’s plan.
With precast concrete, designers have more freedom to make their ideal building without giving up strength or spending too much money.
Improved Lighting and Safety
Precast concrete in warehouses ensures improved lighting and safety. The smooth, reflective surfaces of precast concrete walls enhance natural light distribution within the warehouse, reducing the need for artificial lighting during daytime operations. This not only lowers energy costs but also creates a more pleasant working environment for employees.
Warehouse construction with precast concrete has another big plus: it doesn’t catch fire easily. That means everything inside the warehouse is safer from fire risks. Plus, precast concrete helps keep outside noises from getting in.
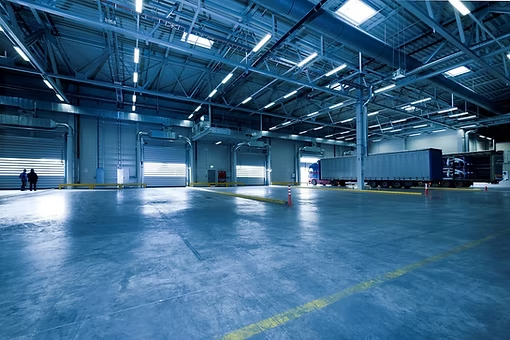
Concrete Building Components for Warehousing
Support columns, beams, and insulated walls are essential precast concrete components for warehouse construction that provide structural strength and durability while also allowing for efficient installation and customization.
Discover how these components contribute to the overall success of a precast concrete warehouse project.
Support Columns
Concrete support columns are crucial for warehouse construction, providing the necessary structural integrity to bear heavy loads. Precast concrete columns offer exceptional strength and durability, making them ideal for supporting the weight of inventory storage systems within a warehouse.
With their ability to withstand significant vertical and lateral loads, precast concrete columns ensure the safety and stability of the entire structure. Additionally, these columns can be customized to specific load capacities and design requirements, offering flexibility in accommodating various warehouse layouts and material handling needs.
Beams
As the construction progresses, another essential component is the beams. Beams play a vital role in bearing the load of the structure and ensuring its strength and durability.
Concrete beams, as part of precast concrete construction, offer exceptional load capacity, contributing to the overall robustness of warehouse structures. This feature makes them an ideal choice for supporting heavy loads commonly found in warehouse environments.
Insulated Walls
Insulated walls made of precast concrete provide excellent thermal resistance, reducing heating and cooling costs for warehouses. These walls also offer sound insulation, creating a quieter and more comfortable working environment.
The use of precast insulated walls aligns with the sustainable construction trend, contributing to energy efficiency and minimizing environmental impact. Additionally, these walls can be customized to meet specific design and architectural requirements, allowing for a combination of aesthetics and functionality in warehouse construction.
Advantages of Using Precast Concrete for Warehouse Construction
Less Maintenance
Using precast concrete for warehouse construction means – less maintenance. The durable nature of precast concrete reduces the need for frequent repairs and upkeep, saving both time and money in the long run.
Additionally, the fire resistance and resilience of precast concrete make it a low-maintenance solution for warehouses. With minimal maintenance requirements, businesses can focus on their operations without worrying about constant upkeep of their warehouse structures.
Cost-Effective
Precast concrete offers reduced long-term maintenance expenses due to its durability and resilience, leading to cost savings over time.
Additionally, the faster construction time of precast concrete warehouses results in reduced labor costs, contributing to overall cost-effectiveness for warehouse construction projects.
These factors make precast concrete a financially viable option for businesses seeking efficient and economical warehouse solutions.
Suitable for LEED Certification
Precast concrete is a sustainable option for warehouse construction, making it suitable for LEED certification. Its efficient production process and ability to minimize waste align with LEED’s environmental criteria.

Additionally, precast concrete contributes to energy efficiency, improves indoor air quality, and provides opportunities for incorporating recycled materials – all factors that can help warehouses meet LEED standards.
Furthermore, the durability and resilience of precast concrete also contribute to its suitability for LEED certification. Its long lifespan reduces the need for replacement or repairs, while its thermal mass properties offer energy-saving benefits such as reduced heating and cooling requirements.
Conclusion
In conclusion, precast concrete offers numerous benefits for warehouse construction. Its time and cost efficiency, structural strength, and design flexibility make it a top choice for modern warehouses.
With examples of successful projects showcasing its advantages, using precast concrete is a durable, cost-effective, and sustainable solution for warehouse construction.
Looking for a trusted partner for your next project? Explore precast concrete offerings from Vintage Cast today.
Recent Posts
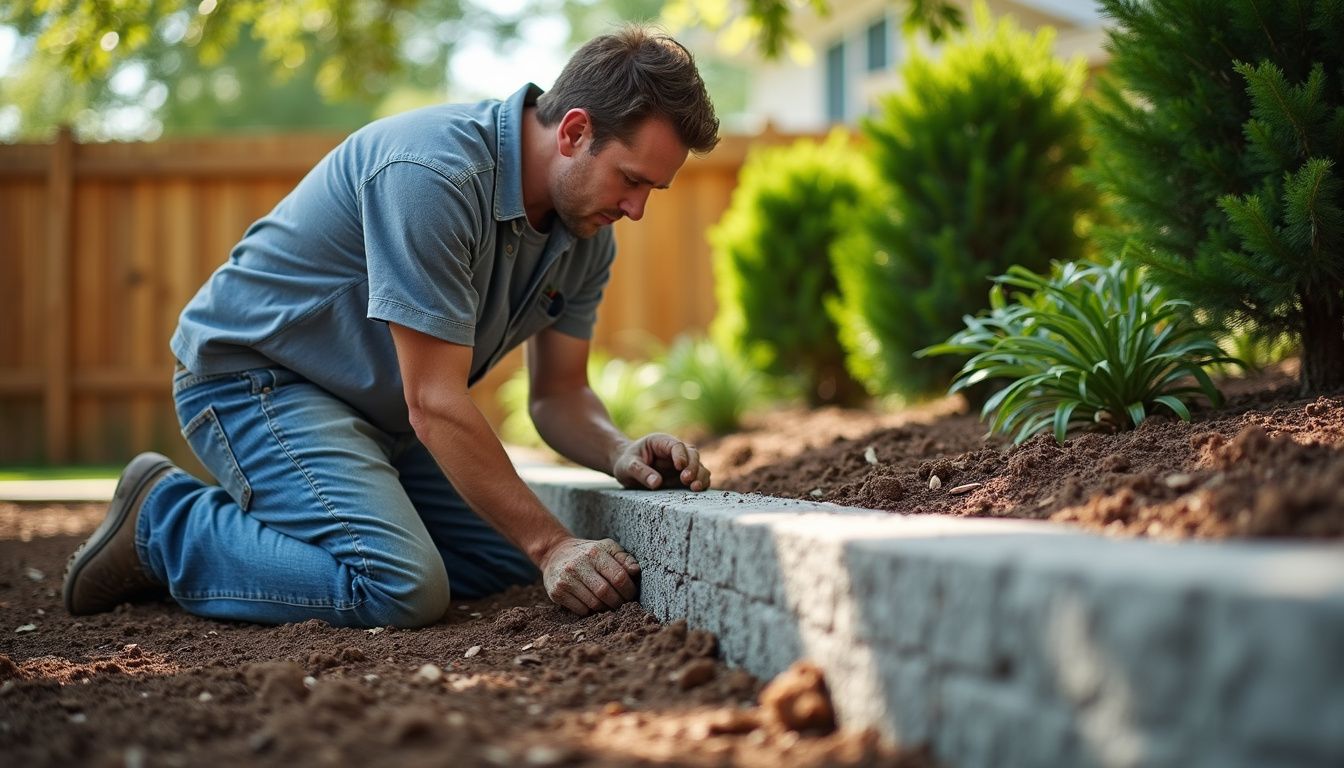
Why Landscaping Pros Prefer Precast Concrete Over Poured-in-Place
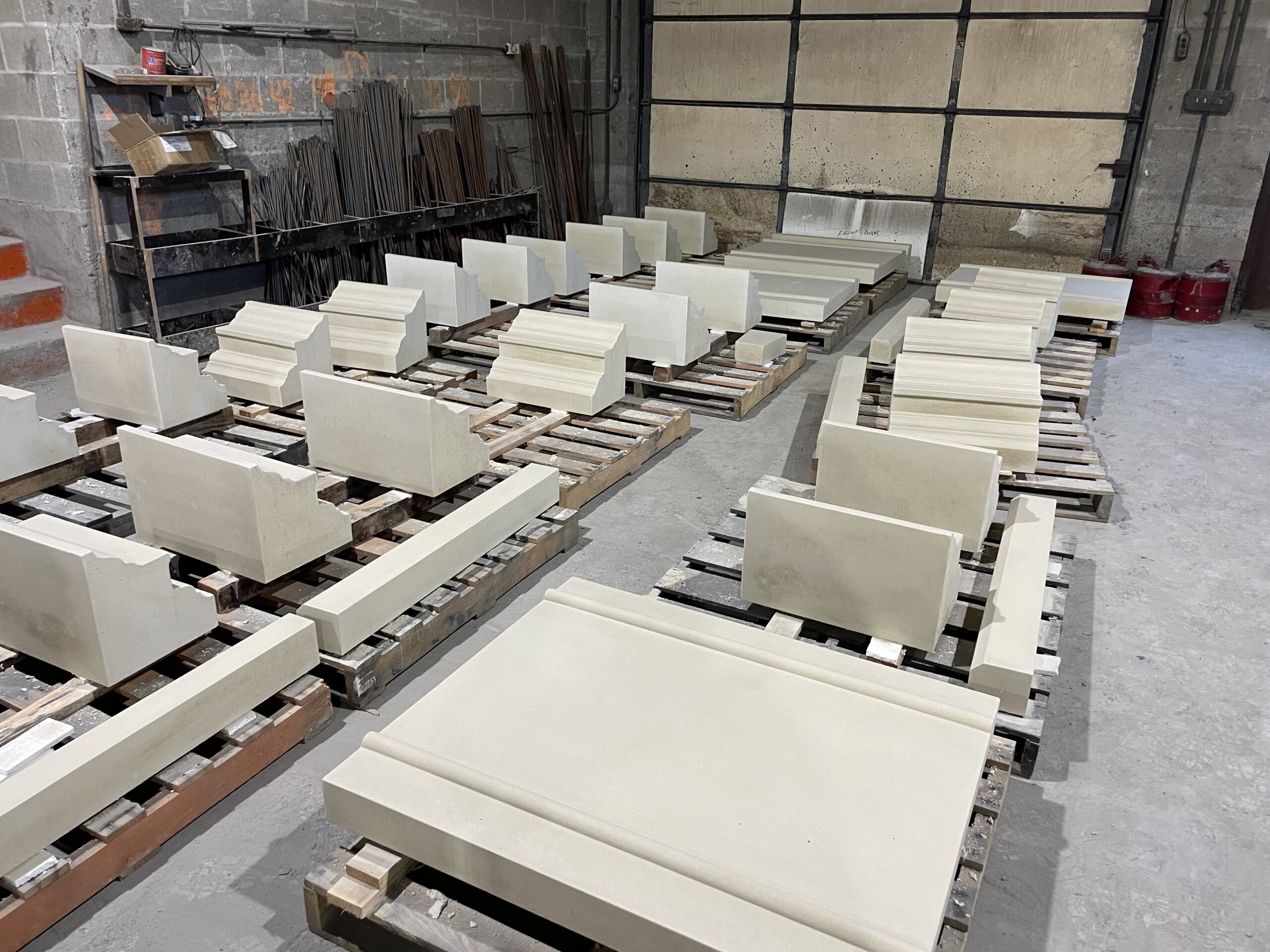
Why & How is Precast Concrete Prestressed?
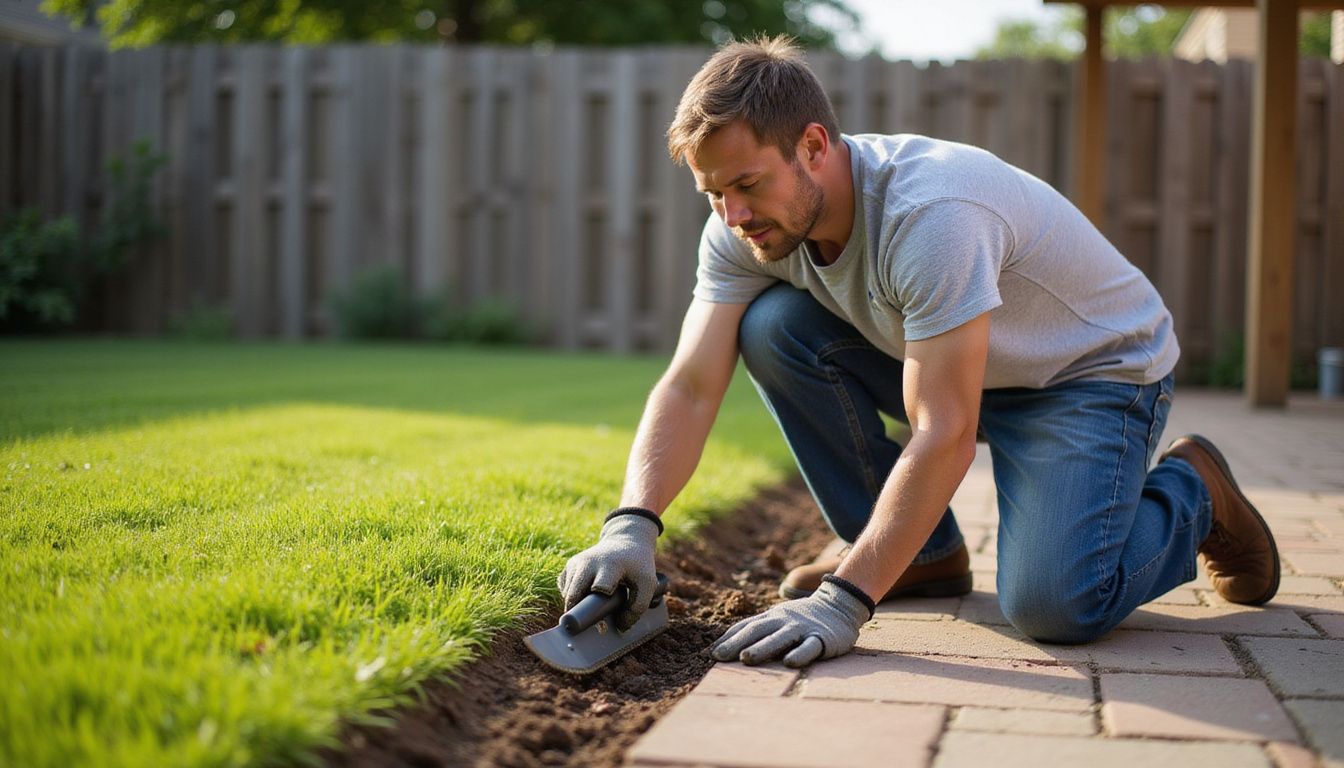