As we build our world, it’s important to ask: is what we’re constructing also good for our planet? Precast concrete stands as one of the most widely used building materials today. This post will dive into its environmental impact and explore whether precast concrete is a friend or foe to the Earth.
Keep reading to uncover the truth behind this construction staple.
Key Takeaways
- Precast concrete is produced off – site in a controlled environment, leading to less waste and pollution during construction.
- It can reabsorb up to 40% of the carbon dioxide emitted during its production phase, helping to reduce its overall environmental impact.
- The use of recycled materials in precast concrete manufacturing conserves natural resources and supports sustainable building practices.
- Precast concrete contributes points toward LEED certification for green building due to features like energy efficiency and lower on-site pollution.
- Faster construction times with precast concrete result in less energy consumption and reduced labor costs, making it an economically efficient choice.
What is Precast Concrete?
Precast concrete is a construction material that is made by casting concrete in a reusable mold, usually off-site, and then cured in a controlled environment. It has gained popularity in the construction industry due to its efficiency and durability.
How is it made?
Precast concrete is a durable building material crafted off-site in controlled factory environments. This process ensures quality, safety, and eco-friendliness by reducing waste and emissions.
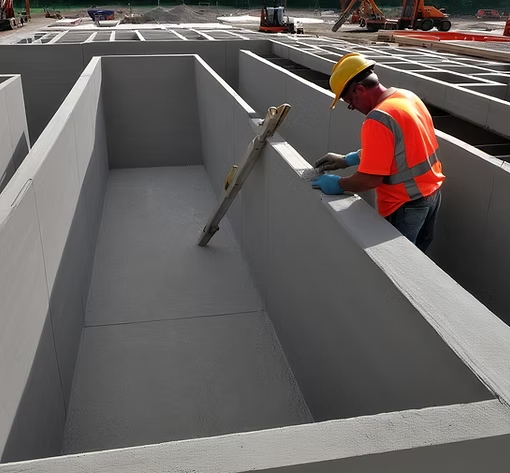
- Manufacturers first design the necessary molds, shaping them to match the specific requirements of the project.
- Workers then prepare these molds with release agents to prevent sticking, ensuring a smooth surface on the finished product.
- The next step involves mixing water, sand, gravel, and cement to create concrete. Proportions are carefully measured for consistency and strength.
- Reinforcements like steel bars or meshes are added to the mixture for extra support where needed, enhancing structural integrity.
- The concrete is poured into prepared molds and is vibrated to eliminate air bubbles which could weaken the structure.
- Once poured, the concrete must cure. Curing happens under controlled temperature and humidity conditions to guarantee proper hardening.
- After curing finishes, skilled workers remove each piece from its mold. They inspect every detail to meet strict industry standards.
- The precast elements are then transported to construction sites. Here they contribute to faster build times and reduced on-site pollution compared to traditional methods.
Its popularity in the construction industry
The popularity of precast concrete in the construction industry has grown significantly due to its numerous advantages. With its ability to be produced off-site and transported for use, it has become a preferred choice for large-scale projects.
Its consistency and durability make it ideal for construction across various sectors, including residential, commercial, and infrastructure development. Additionally, its versatility allows architects and engineers to create innovative designs while maintaining structural integrity.
Precast concrete’s popularity is also attributed to its cost-effectiveness. It reduces construction time by allowing simultaneous on-site preparation while components are manufactured off-site.
Environmental Impact of Precast Concrete
The production process of precast concrete can result in high carbon emissions and waste generation. However, there is potential for precast concrete to absorb carbon dioxide over its lifecycle, reducing its overall environmental impact.
Production process and emissions
Precast concrete is manufactured in a controlled environment, reducing the potential for environmental damage. This process minimizes on-site waste and pollution, as well as the release of harmful emissions.
Additionally, precast concrete production reduces energy consumption and carbon dioxide emissions when compared to traditional cast in-situ methods. Notably, this method offers a more resource-efficient and eco-conscious approach to construction.
The manufacturing of precast concrete also involves lower water usage and decreased air pollution within factory settings, making it environmentally preferable over conventional construction processes.
Waste and pollution
During the production process, precast concrete generates minimal waste and pollution. The controlled manufacturing environment reduces the risk of air and water contamination typically associated with on-site construction activities.
Precast concrete also minimizes pollution by using recycled materials in its production, which helps conserve natural resources and reduce landfill waste.
The use of precast concrete can significantly decrease the amount of construction-related pollution released into the environment. With sustainable practices and reduced emissions during its production, precast concrete proves to be an environmentally responsible choice for construction projects.
Potential for carbon dioxide absorption
Concrete naturally absorbs carbon dioxide from the atmosphere over time, a process known as carbonation. This occurs as the concrete’s calcium compounds react with CO2 to form calcium carbonate, effectively locking in the carbon.
In fact, precast concrete can reabsorb up to 40% of the carbon emitted during its production phase, contributing to reduced environmental impact.
Furthermore, this absorption continues throughout the structure’s entire lifespan. As a result, precast concrete not only plays a role in reducing its own carbon footprint but also actively contributes to mitigating atmospheric CO2 levels over time.
Sustainable Practices in Precast Concrete
This section will explore the sustainable practices in precast concrete, including the use of recycled materials, reduced construction time and on-site pollution, as well as LEED certification and points.
These initiatives are crucial in reducing the environmental impact of precast concrete in the construction industry.
Use of recycled materials
Precast concrete incorporates recycled materials, reducing the demand for virgin resources and minimizing environmental impact. Recycled aggregates like crushed concrete and reclaimed steel reinforcement are commonly used in precast production, contributing to sustainable building practices and decreasing the carbon footprint of construction projects.
Additionally, incorporating recycled content into precast concrete addresses concerns about waste generation while promoting a circular economy within the construction industry.
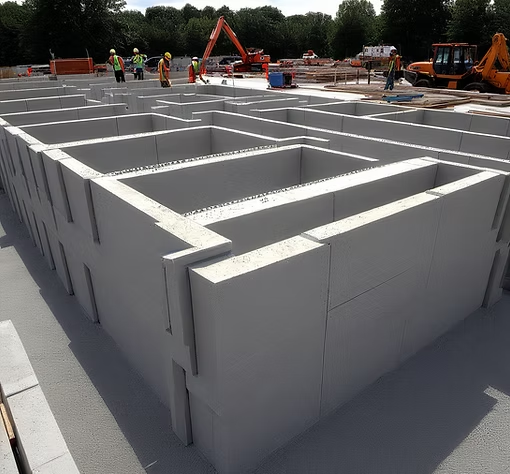
Reduced construction time and on-site pollution
Precast concrete leads to reduced construction time and lowered on-site pollution. The manufacturing process occurs in a controlled environment, minimizing weather-related delays common in traditional onsite construction.
With the ability to concurrently handle site preparation and precast installation, projects can be completed up to 50% faster than conventional methods. Additionally, this offsite production mitigates noise, dust, and waste at the construction site, contributing to a cleaner and safer working environment for laborers.
Moreover, by reducing their reliance on heavy machinery and shortening project timelines, precast concrete minimizes fuel consumption and emissions associated with onsite construction activities.
LEED certification and points
To achieve LEED certification, construction projects need to meet specific criteria related to sustainability and environmental impact. Precast concrete can contribute points towards LEED certification due to its eco-friendly features such as reduced construction time, lower on-site pollution, and use of recycled materials.
Additionally, the durability of precast concrete reduces the need for future renovations or replacements, further contributing to the sustainable building design. By using precast concrete in construction projects, builders can earn valuable LEED points while also reducing their carbon footprint.
LEED certification rewards buildings that prioritize energy efficiency and environmental sustainability. Precast concrete’s ability to reduce heating and cooling costs substantially aligns with these principles.
Conclusion
In conclusion, precast concrete offers significant environmental benefits. It reduces construction waste and pollution while allowing for the use of recycled materials. Its manufacturing process also leads to reduced on-site pollution and safer working conditions for construction workers.
Overall, precast concrete demonstrates a commitment to eco-conscious building practices and supports sustainability in the construction industry.
FAQs
1. What does precast concrete mean for the environment?
Precast concrete plays a role in ecofriendly construction by being durable and having the potential for a low carbon footprint compared to other building materials.
2. Is using precast concrete in building considered green construction?
Yes, when used responsibly, precast concrete can be part of green construction thanks to its energy efficiency and material safety that contribute to sustainability.
3. Can precast concrete improve the resilience of the construction industry?
Absolutely! Precast concrete is known for its durability, making it a resilient choice for buildings and helping reduce environmental impact over time.
4. How does the carbon footprint of precast concrete compare to other materials?
The carbon footprint of precast concrete can be lower than traditional on-site poured materials due to more controlled manufacturing processes leading to less waste.
5. Are there any sustainability concerns with using precast concrete?
While there are environmental concerns with all types of construction, focusing on eco-conscious building practices helps mitigate negative effects and advances sustainability efforts with materials like precast concrete.
Recent Posts
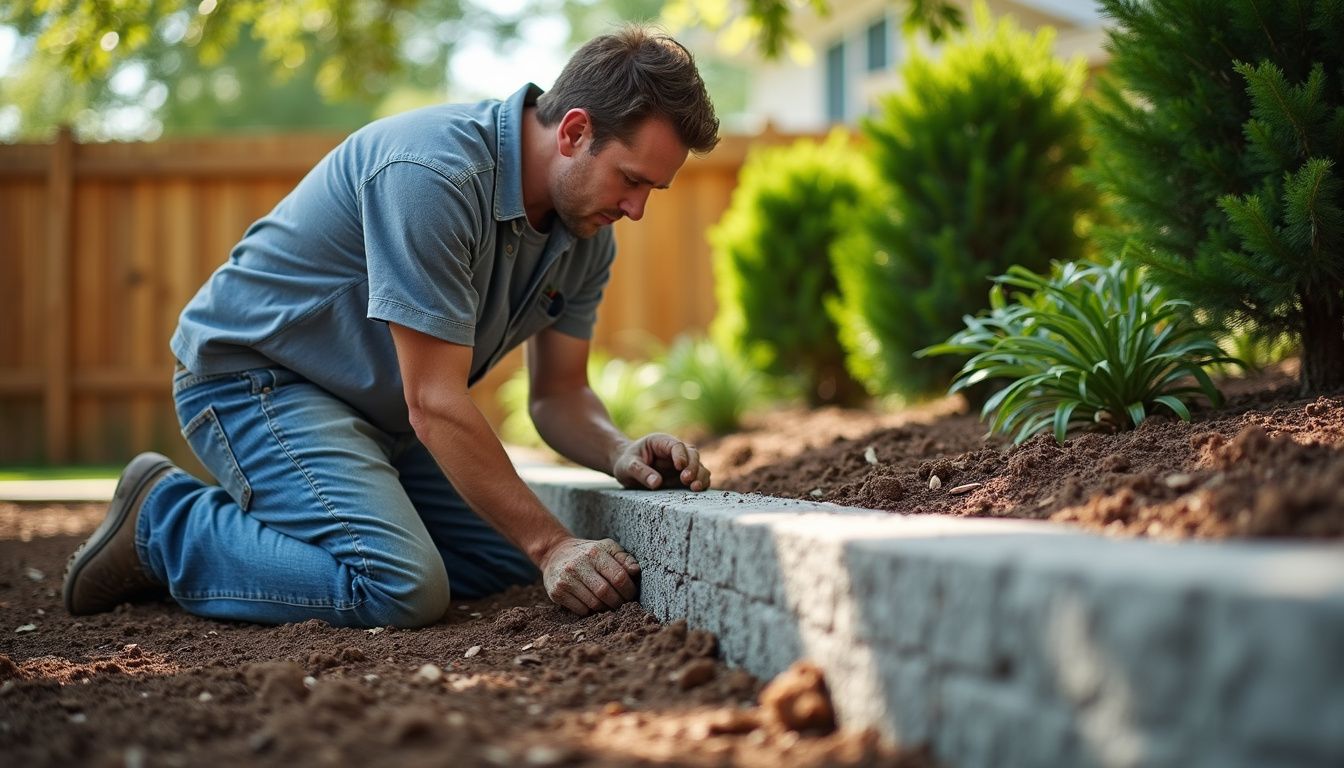
Why Landscaping Pros Prefer Precast Concrete Over Poured-in-Place
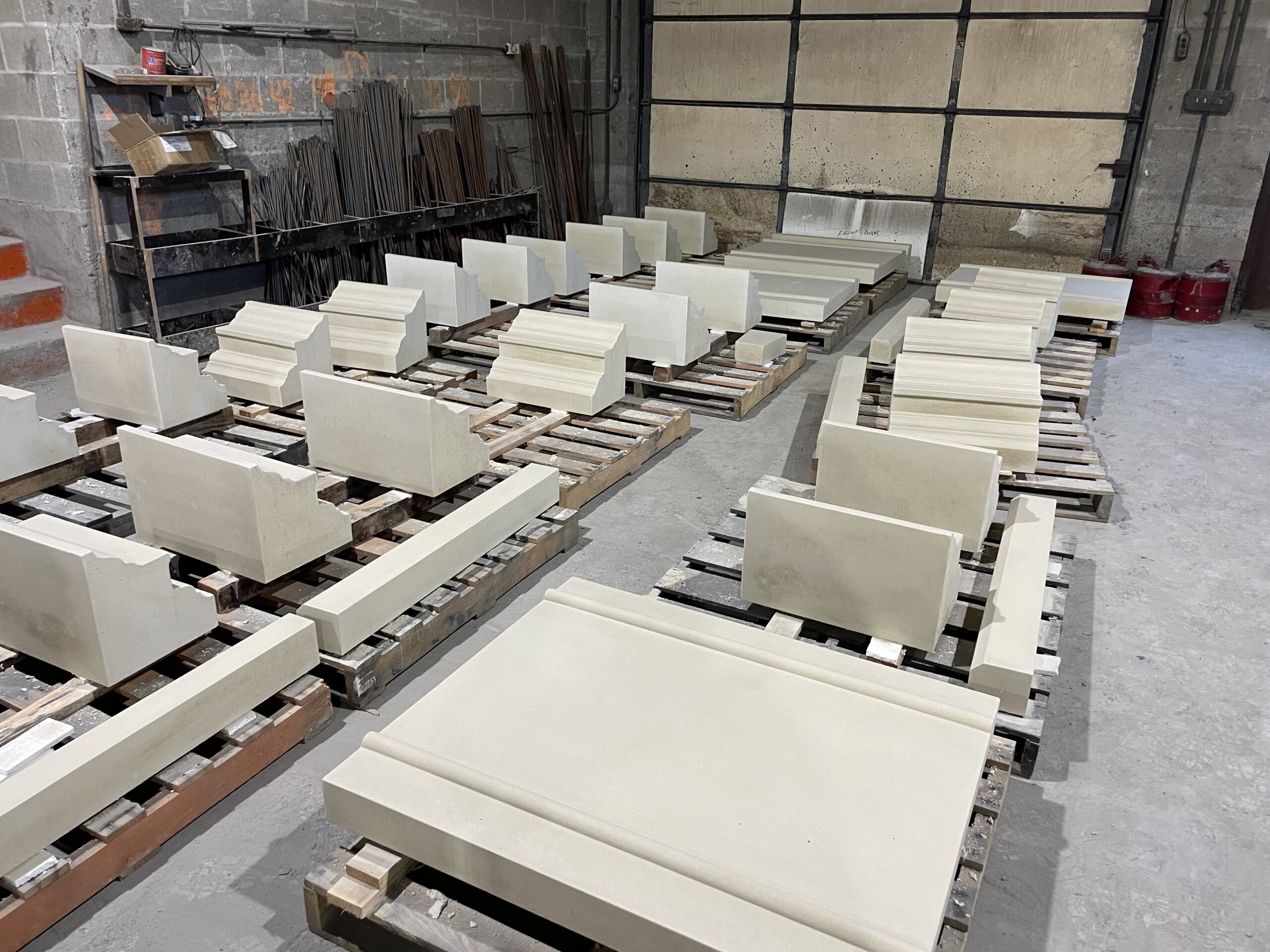
Why & How is Precast Concrete Prestressed?
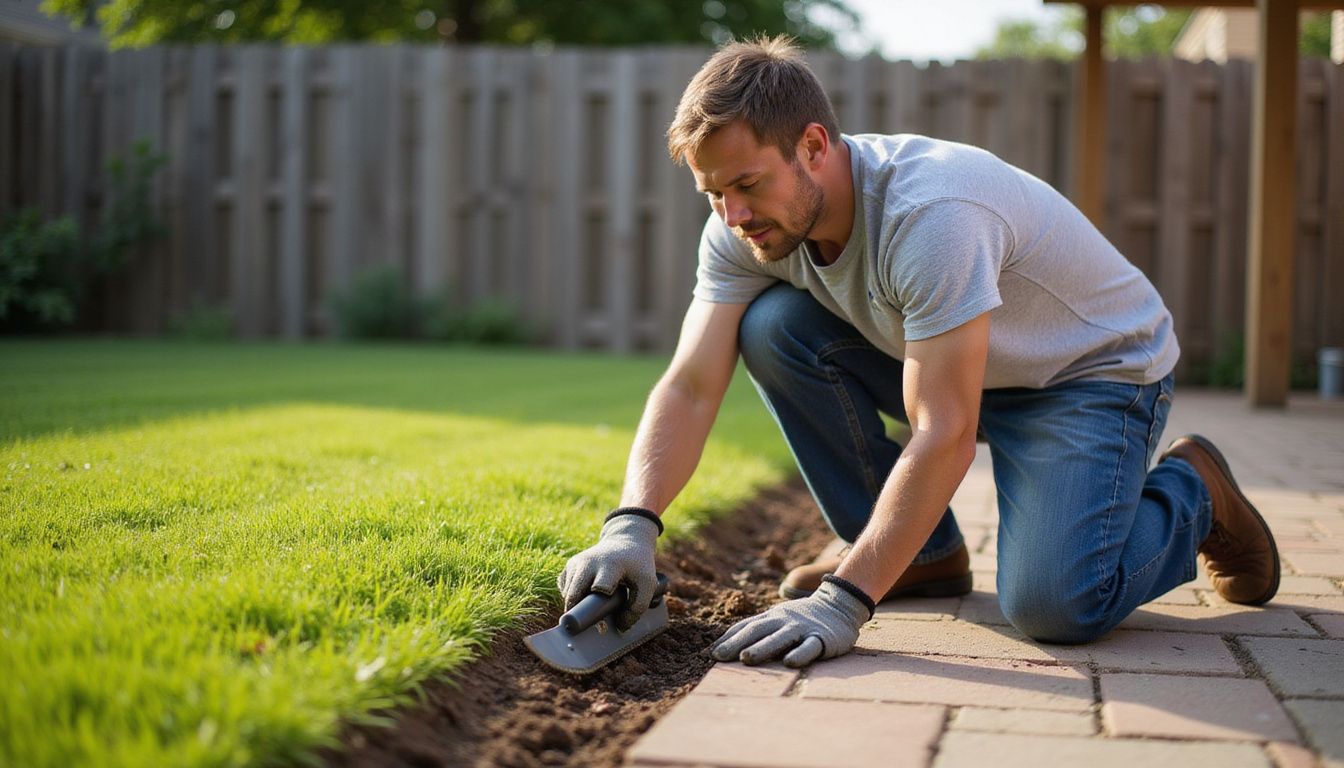