When planning a construction project, cost savings are a top priority. Precast concrete structures can be up to 23 percent cheaper than traditional onsite pouring. Our guide will reveal how precast concrete offers financial benefits without skimping on quality or durability.
Key Takeaways
- Precast concrete can save up to 23 percent in costs compared to traditional onsite pouring.
- It offers cost benefits like reduced transportation fees, faster construction times avoiding delays, and less need for expensive finishing work on site.
- The controlled factory environment of precast concrete results in consistent high quality and durability that stand up against fire, moisture, and pests.
- Using precast concrete streamlines processes by allowing other site preparations to occur simultaneously with manufacturing, reducing overall project timelines.
- While initial costs might vary due to design intricacies or transport logistics, the long – term savings from using precast concrete often make it a more economical choice.
What is Precast Concrete?
Precast concrete is a durable and versatile construction material often used to build walls, slabs, and other structural components. It’s created by casting concrete in a reusable mold or “form” which is then cured in a controlled environment, transported to the construction site, and lifted into place.
Unlike traditional cast-in-place concrete that is poured directly at the job site, precast concrete units are manufactured offsite in a factory setting. This allows for greater control over the material quality and workmanship.
The process of creating precast concrete involves pouring high-quality concrete into molds with a specific design meant for repeated use. After the concrete hardens, it’s removed from the form ready for transport—fully dried and shaped according to its intended purpose.
The efficiency gained through this method makes it financially advantageous because it lowers manufacturing costs while ensuring consistency across multiple pieces. Precast products range from simple structures like pipes or road barriers to elaborate architectural elements such as ornate facades or sturdy beams capable of bearing heavy loads—all contributing to more affordable building alternatives with significant savings on both time and money.
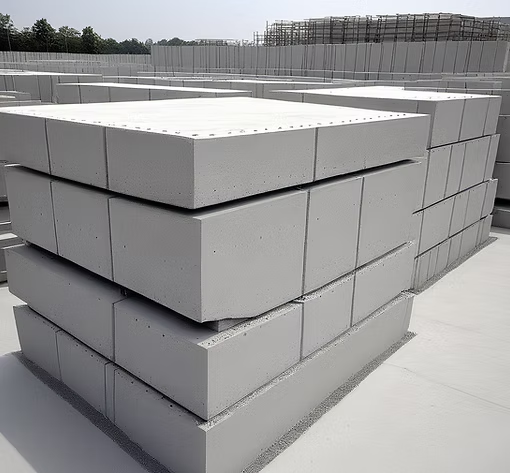
How Precast Concrete Saves Money
Precast concrete saves money through reduced transportation costs, versatility in different industries, prevention of delays, superior quality, and enhanced safety.
Reduced Transportation Costs
Using precast concrete can result in significant cost savings due to reduced transportation expenses. Compared to traditional on-site pouring, precast concrete products save money by requiring fewer workers, vehicles, and tools for transportation.
The lighter weight of precast components also contributes to lower transportation costs, as it reduces fuel consumption and allows for more efficient logistics.
Furthermore, the use of precast concrete minimizes onsite congestion, leading to reduced traffic and quicker project completion. These factors combined make precast concrete a cost-effective choice that provides value for money while lowering overall construction material expenses.
Versatility in Different Industries
Precast concrete’s versatility extends across various industries, including residential, commercial, industrial, and infrastructure. For instance, in the construction industry, precast concrete is used for walls, floors, and other structural components due to its adaptability and cost-effectiveness.
In the transportation sector, it’s employed in building bridges and highways with durable precast elements. Moreover, in the utilities sector, precast concrete contributes to cost-efficient construction of water treatment facilities and drainage systems.
Furthermore, the agricultural industry benefits from precast concrete through applications such as farm buildings and storage structures. This adaptability makes precast concrete a practical choice for diverse projects requiring efficient material usage while still adhering to budget constraints.
Prevention of Delays
Precast concrete helps prevent delays in construction projects. With precast components being manufactured off-site, they can be produced in parallel with other on-site preparations.
This ability significantly reduces the overall construction timeline and minimizes the risk of project delays. Additionally, precast elements can be installed quickly once delivered to the site, further mitigating potential setbacks.
The efficiency of precast concrete also contributes to avoiding weather-related interruptions common in traditional on-site pouring methods. Because precast units are fabricated indoors, they are less susceptible to weather conditions that could delay progress during construction.
Superior Quality
Precast concrete offers superior quality due to the controlled environment of the manufacturing process, resulting in consistent and high-quality products. The use of precast concrete also ensures precise measurements and replicable finishes, reducing errors and enhancing structural integrity.
Additionally, precast concrete components undergo rigorous testing to meet industry standards, ensuring durability and reliability for long-term performance.
The superior quality of precast concrete extends to its resistance to environmental factors, including fire, moisture, and pests. Moreover, precast components often incorporate special additives that enhance strength and durability while reducing maintenance needs over time.
Enhances Safety
Precast concrete enhances safety through its durable and uniform construction, reducing the risk of structural failure and potential hazards. With precast concrete’s factory-controlled processes, the risk of accidents on-site is minimized, ensuring a safer working environment for construction teams.
Additionally, precast elements are designed to withstand harsh environmental conditions and have excellent fire resistance capabilities, providing long-term safety benefits for building occupants.
Furthermore, precast concrete components can be manufactured with embedded features such as handrails or connections that enhance overall safety during installation and use. These unique characteristics make precast concrete an ideal choice for projects where safety is a top priority.
Factors Affecting Precast Concrete Costs
Shape, dimensions, and weight, delivery and excavation, engineering fees and installation, finishing and design, as well as additional costs are all factors that can impact the overall cost of using precast concrete.
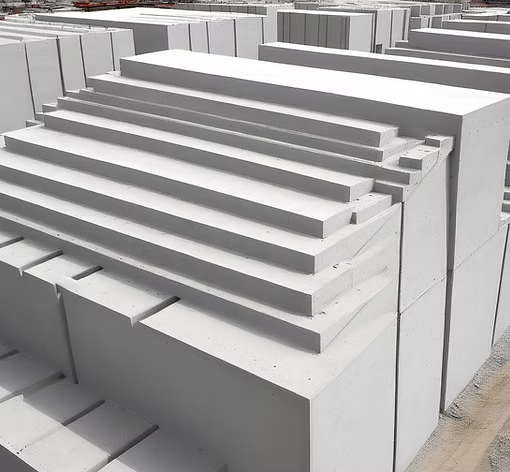
Shape, Dimensions, and Weight
The shape, dimensions, and weight of precast concrete components greatly impact the overall cost. Precast products can be customized to fit specific project requirements, reducing waste and material costs.
Moreover, precise measurements result in accurate installation, further lowering labor expenses. Additionally, the reduced weight of precast elements minimizes transportation costs and simplifies onsite handling.
Engineers carefully design precast concrete components to meet exact specifications, ensuring efficient use of materials and lower overall costs. The ability to customize shapes and sizes allows for more efficient construction processes while minimizing excess materials.
Delivery and Excavation
Delivery and excavation play a crucial role in determining the overall cost of precast concrete. Efficient delivery methods, coupled with strategic excavation planning, can significantly reduce transportation costs and prevent delays during construction.
By carefully scheduling deliveries and optimizing transportation routes, businesses can save on expenses related to fuel, labor, and vehicle maintenance. Additionally, precise excavation practices ensure minimal disruption to the surrounding area while preparing the site for efficient installation of precast concrete components.
Understanding the impact of delivery and excavation on precast concrete costs is essential for maximizing savings throughout the construction process. Proper coordination of logistical operations and meticulous excavation planning are key factors in achieving cost-effective outcomes when utilizing precast concrete solutions.
Engineering Fees and Installation
Precast concrete reduces engineering fees and installation costs due to its streamlined production process. The modular nature of precast components minimizes on-site labor, resulting in fewer hours billed by engineers and lower installation expenses.
Additionally, the efficiency of precast concrete manufacturing translates into reduced construction time, further cutting down on engineering fees. With a simplified installation process, precast concrete also saves money on heavy equipment usage and workforce deployment during assembly.
Furthermore, the precision and consistency of precast concrete elements reduce unexpected project delays and adjustments that can drive up engineering fees. Such predictability allows for accurate planning and scheduling upfront without the need for costly last-minute modifications or redesigns.
Finishing and Design
Precast concrete offers a wide range of finishing and design options, including various textures, colors, and patterns. This allows for customization to meet specific aesthetic preferences and project requirements.
By incorporating these features during the manufacturing process, precast concrete products can be delivered and installed with minimal site finishing work, reducing overall construction time and costs while maintaining high-quality aesthetics.
In addition to visual customization, precast concrete also enables flexibility in design elements such as shapes, dimensions, and surface treatments. With precise engineering and casting techniques, intricate designs can be achieved to enhance architectural appeal without compromising structural integrity or budget constraints.
Additional Costs
Additional costs associated with precast concrete include:
- Finishing and Design: The cost of finishing and adding design elements to precast concrete products can vary based on the complexity and intricacy of the design. This includes surface treatments, coloring, and other decorative finishes.
- Engineering Fees and Installation: There may be additional expenses related to hiring engineers for custom designs or unique project requirements. Moreover, the installation process for precast concrete components may incur labor costs or specialized equipment rentals.
- Shape, Dimensions, and Weight: The shape, dimensions, and weight of precast concrete components can impact the overall cost due to the need for custom molds, heavy lifting equipment, or complex handling procedures.
- Delivery and Excavation: Transportation expenses for delivering precast concrete products to the construction site play a significant role in determining the total cost. Additionally, excavation costs for preparing the site to accommodate precast elements should be considered.
- Maintenance Costs: While precast concrete is known for its durability and low maintenance requirements, there might still be ongoing maintenance expenses over time to ensure structural integrity and longevity.
Conclusion: Is Precast Concrete Worth the Cost?
In conclusion, precast concrete offers significant cost savings compared to traditional in-place pouring. It reduces transportation costs, prevents delays, and ensures superior quality while enhancing safety.
Factors such as shape, dimensions, weight, delivery and excavation can affect the overall cost of precast concrete. However, when considering long-term benefits and efficiency, precast concrete proves to be a budget-friendly and efficient construction material choice.
FAQs
1. What is precast concrete, and how can it save on construction costs?
Precast concrete is concrete that’s cast into a specific shape at a factory, which can be more cost-effective than casting in place on the construction site because of factory efficiency.
2. Is using precast concrete slabs cheaper than other methods?
Using precast concrete slabs often leads to lower costs compared to traditional cast-in-place methods due to reduced labor expenses and faster installation times.
3. Can precast concrete help with reducing overall building expenses?
Yes, since precast concrete is prefabricated in controlled environments, it contributes to reduced building material expenses and can offer budget-friendly options for constructing walls or structural components.
4. Are there cost savings when using precast versus other types of construction materials?
Precast construction usually provides cost savings by being a more efficient alternative; saving time during the build process typically translates directly into overall construction cost reductions.
5. How do builders calculate the potential savings from using precast concrete panels?
Builders often use a building cost estimator considering factors like linear foot pricing of floor panels and structural elements to determine if opting for prefabricated precast elements will be more cost-efficient for their project.
Recent Posts
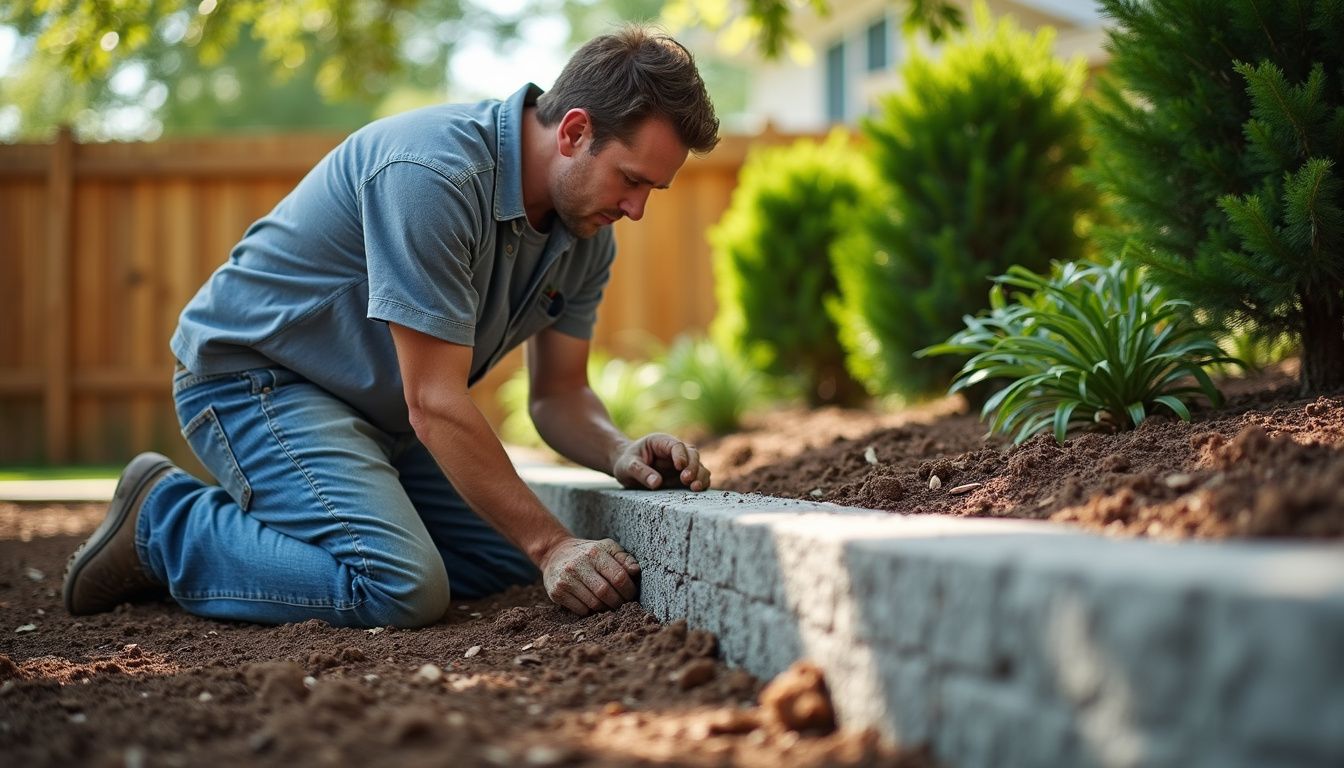
Why Landscaping Pros Prefer Precast Concrete Over Poured-in-Place
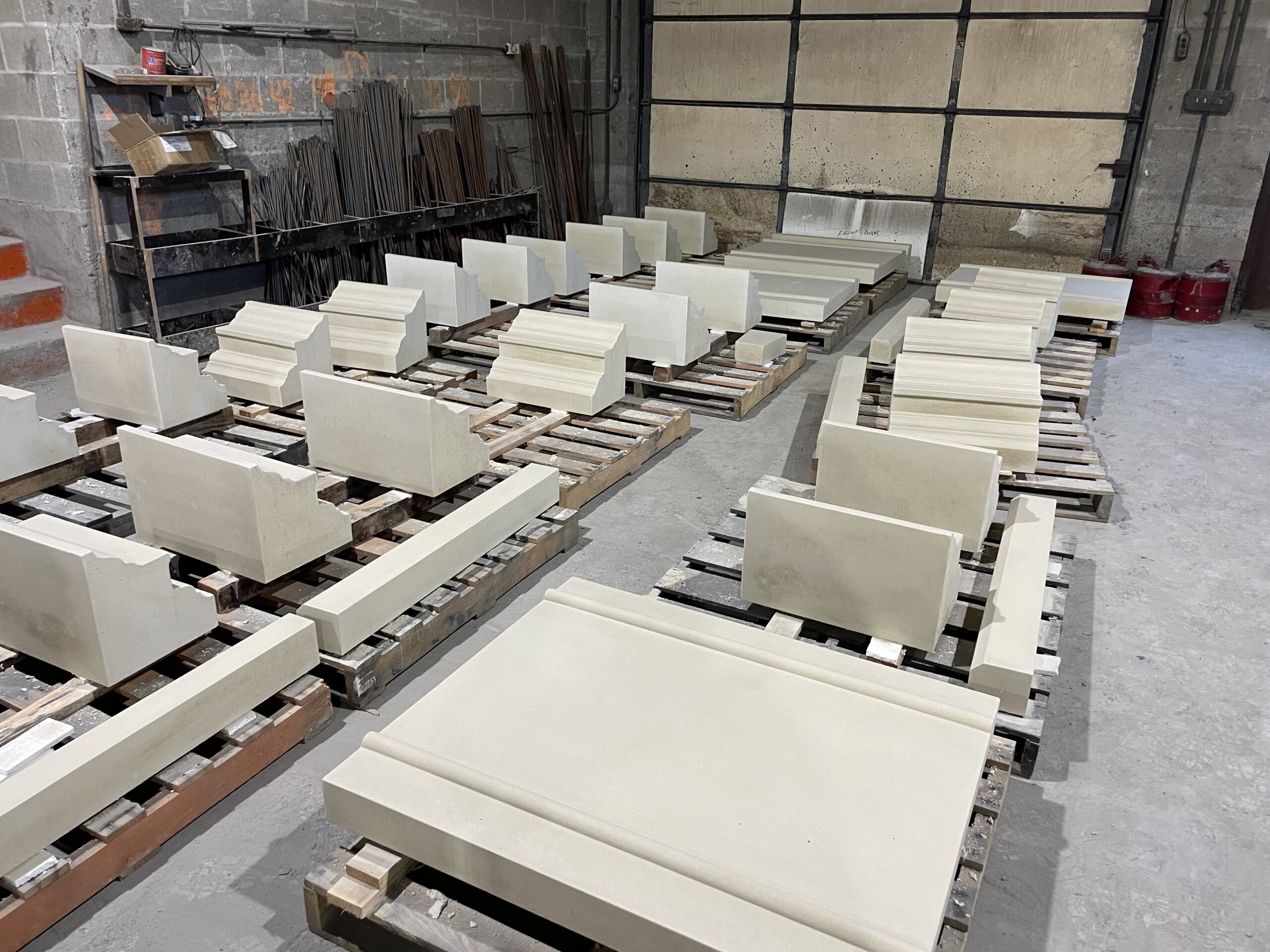
Why & How is Precast Concrete Prestressed?
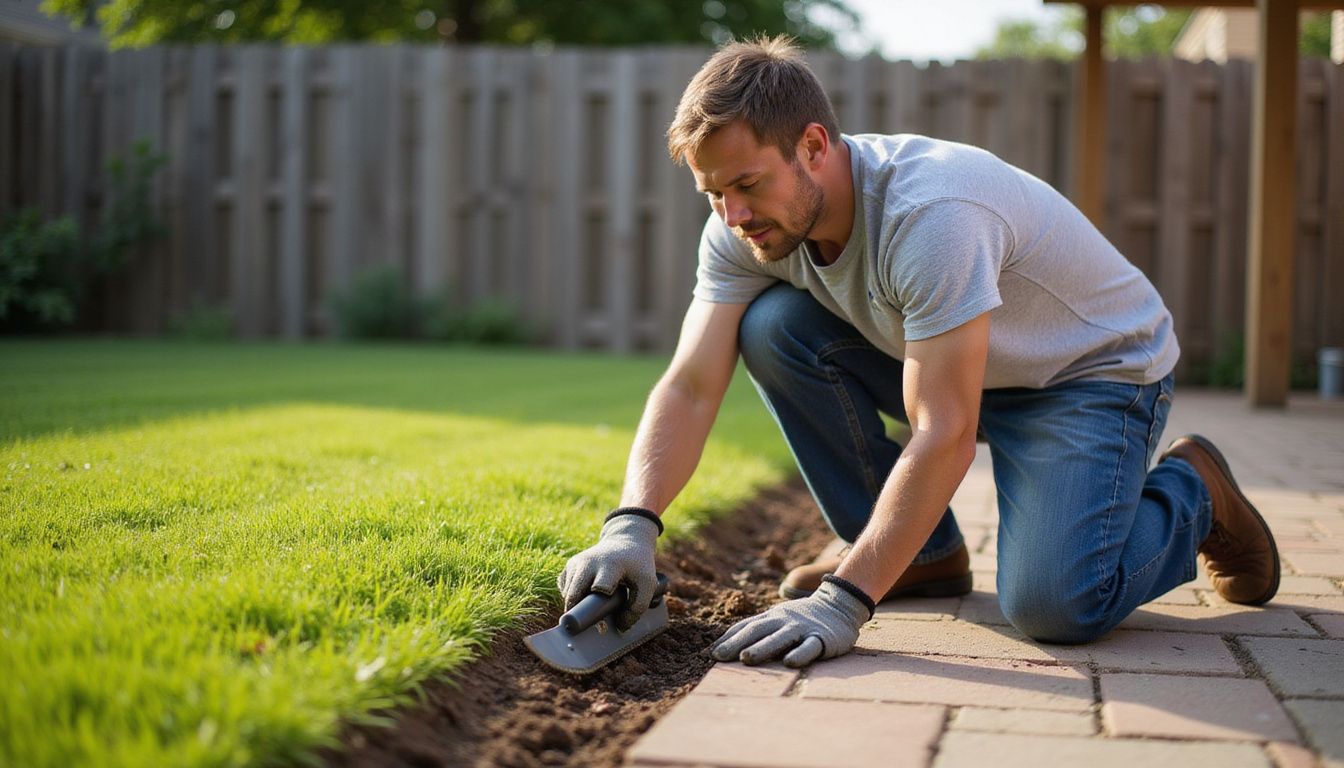