When deciding to build a home, cost is a huge factor for many of us. It’s often believed that concrete homes are pricier than those made with wood framing. This post will compare the costs and benefits of building with concrete versus traditional materials.
Key Takeaways
- Concrete homes often have higher upfront costs due to specialized labor and material expenses; for example, concrete can cost $100 to $150 per cubic yard, but these houses save money over time with lower maintenance and energy efficiency.
- Energy savings in concrete houses come from the material’s insulation properties, which help maintain consistent temperatures and reduce heating and cooling bills.
- Different types of concrete homes like ICFs, prefab or precast models, and spider tie construction offer varying benefits such as faster build times and increased durability against natural disasters.
- The average building cost for a concrete home is between $120 to $180 per square foot, potentially 4 to 8 percent more than traditional wood frame constructions
- When planning a concrete house project, it’s crucial to work with experienced contractors who can navigate the complexities of cement-based construction while optimizing design elements for both aesthetic appeal and practicality.
The Cost Comparisons of Building a Concrete House vs Traditional Houses
Building a concrete house can be more cost-effective in terms of labor and material costs compared to traditional houses, especially when considering long-term energy efficiency. Different types of concrete houses also offer varying cost benefits.
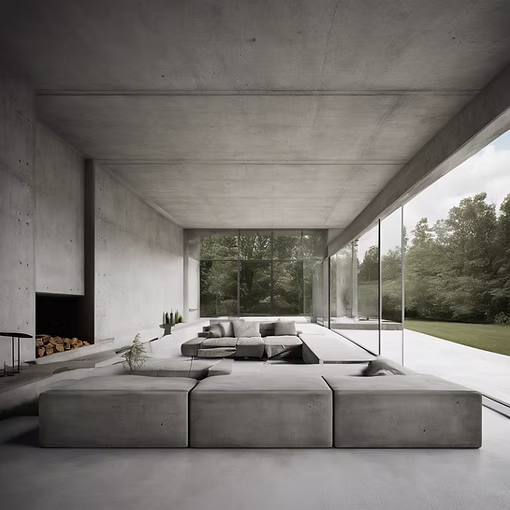
Labor costs
Hiring skilled professionals to build a concrete house usually means higher labor expenses. Concrete construction requires specialized tools and expertise, meaning you might pay more for the workforce compared to traditional home construction.
These workers mix, pour, set, and finish concrete, tasks that often take longer and are more complex than nailing lumber together. As a result, the labor costs contribute significantly to the overall price of building with cement.
The cost-effectiveness in labor for concrete homes can depend on factors like location and design complexity. In urban areas where labor rates are higher, or for houses with intricate designs requiring detailed formwork, your expenses will rise accordingly.
Material costs
When considering the material costs for building a concrete house, it’s essential to note that the primary materials used are concrete, steel reinforcement, and insulation. The cost of these materials can vary based on location and quality.
Concrete prices typically range from $100 to $150 per cubic yard, while steel reinforcement costs around $0.50 to $1.50 per square foot. Additionally, insulation costs for an ICF house average around $1.00 to $2.00 per square foot.
The expense of these materials contributes significantly to the overall construction expenses of a concrete house compared to traditional stick-built homes using lumber and drywall as primary components in construction.
Energy efficiency
Concrete houses are known for their energy efficiency, as the material provides excellent insulation, reducing heating and cooling costs. Concrete’s thermal mass helps regulate indoor temperatures by absorbing and storing heat during the day and releasing it at night.
This can result in significant energy savings over time, making concrete homes a cost-effective choice for homeowners looking to reduce their utility bills. Additionally, concrete’s durability means that the need for frequent maintenance is minimized, further contributing to long-term energy efficiency and cost savings.
Types of Concrete Houses
Concrete houses come in various forms, including concrete masonry, ICF, precast concrete homes, and spider tie concrete houses. Each type offers unique benefits in terms of cost-effectiveness and durability.
Concrete Masonry
Concrete masonry involves using concrete blocks or bricks to construct the walls of a house. These materials offer durability and stability, making them an attractive option for homeowners seeking long-term resilience.
Concrete masonry homes can also provide excellent insulation, reducing energy costs over time. Additionally, these structures can withstand extreme weather conditions, offering peace of mind to homeowners in areas prone to hurricanes or tornadoes.
Insulated Concrete Forms (ICF)
ICFs offer an energy-efficient and durable alternative to traditional building methods. ICFs are stackable, interlocking forms made of expanded polystyrene (EPS) or other insulating foam that are filled with concrete.
The resulting structure provides exceptional thermal insulation, reducing heating and cooling costs. Additionally, ICF construction offers improved soundproofing capabilities and enhances the structural integrity of homes, making them more resistant to natural disasters.
Homes built with ICFs often require smaller HVAC systems due to their superior energy efficiency.
Embracing ICFs is a cost-effective solution for homeowners seeking long-term savings in both maintenance costs and energy expenses. Investing in this sustainable building method can also add value to the property in the long run.
Precast Concrete Homes
When considering alternative concrete construction methods, prefab or precast concrete homes offer a cost-effective and efficient solution. Prefabricated concrete panels are manufactured off-site, reducing on-site labor costs and accelerating the construction timeline.
This method of construction also allows for precise quality control, minimizing material wastage and ensuring consistency in the building process. Additionally, precast concrete homes have superior thermal performance due to the insulation integrated into the panels during manufacturing, contributing to long-term energy efficiency and lower utility costs.
These homes offer a faster build time as they can be constructed regardless of weather conditions since much of the work is done indoors. The use of prefabricated or precast components can also result in reduced overall project expenses despite potentially higher initial material costs.
Spider Tie Concrete Houses
Spider Tie concrete houses offer an innovative and cost-effective way to build durable and energy-efficient homes. These structures utilize a patented system of pre-engineered, steel-reinforced concrete panels that are interconnected using high-strength fiber straps.
The construction process is efficient, reducing labor costs and construction time while providing exceptional strength and durability. Spider Tie concrete houses also offer superior insulation properties, ensuring energy efficiency and long-term savings on heating and cooling expenses.
The unique design of Spider Tie concrete houses allows for versatile architectural options, providing homeowners with the flexibility to create custom layouts and designs. The use of this cutting-edge building method can result in significant long-term maintenance savings due to its resistance to natural elements such as wind, fire, and moisture.
Pros and Cons of Building a Concrete House
Building a concrete house offers advantages such as durability, energy efficiency, and resistance to natural disasters. However, it may also have drawbacks like the initial cost of construction and limited design flexibility.
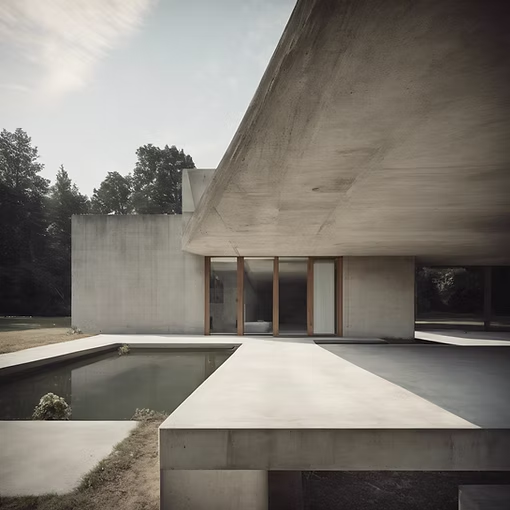
Advantages
Concrete houses offer several advantages over traditional stick-built homes. They are more durable and require less maintenance over time, making them a cost-effective choice in the long run.
Additionally, concrete houses provide better insulation, resulting in energy efficiency and lower utility bills. Moreover, their robust construction makes them resistant to severe weather conditions such as hurricanes and tornadoes, ensuring greater safety for homeowners.
Furthermore, concrete homes have higher resale value due to their durability and longevity, making them a wise investment for those looking for a sustainable and resilient housing option.
Disadvantages
Higher initial costs and longer construction timelines are common drawbacks of building a concrete house.
Concrete homes tend to have higher upfront expenses due to the material’s cost, as well as specialized labor requirements for construction. Additionally, the longer curing time for concrete can extend the overall building timeline, potentially delaying occupancy in comparison to traditional stick-built homes.
Furthermore, the inflexibility of design options in concrete construction can be seen as a disadvantage compared to other building methods. Unlike wood-framed houses that allow for more flexible modifications and additions post-construction, making alterations to a concrete house may be more challenging and costly due to its structural integrity.
Tips for Building a Concrete House
When building a concrete house, it’s important to hire the right contractor who has experience with concrete construction. Additionally, calculating costs, choosing exterior finishes, and considering additional design elements are all crucial aspects to consider when building a concrete house.
Hiring the right contractor
When hiring a contractor to build a concrete house, look for professionals with experience in concrete construction. Ensure the contractor is licensed, bonded, and insured to protect yourself from liability and subpar workmanship.
Request detailed estimates from multiple contractors to compare costs and services before making a decision. Discuss the timeline for completion and any potential challenges they foresee during the construction process.
Calculating costs
Calculating the costs of building a concrete house involves factoring in labor, material, and energy efficiency expenses. The average cost of constructing a concrete home ranges from $120 to $180 per square foot, which is generally 4 to 8 percent higher than traditional stick-built houses.
When estimating expenses for a concrete house, homeowners should consider long-term maintenance savings against initial construction investment as these homes are known for their durability and low maintenance requirements over time.
Choosing exterior finishes
One essential aspect when building a concrete house is choosing the right exterior finishes. Concrete houses offer versatile options for exterior finishes, including stucco, stone veneer, brick, or even wood siding.
It’s important to consider factors like durability, maintenance requirements, and the overall aesthetic appeal of each finish. Stucco is a popular choice for concrete homes due to its longevity and resistance to fire and moisture.
Stone veneer adds an elegant touch and enhances the curb appeal of the property while requiring minimal maintenance. Additionally, brick offers excellent durability and can contribute to energy efficiency in concrete houses.
Considering additional design elements
Concrete houses offer a wide range of design possibilities, allowing homeowners to incorporate various architectural elements. By integrating features such as large windows, skylights, or open floor plans, concrete homes can maximize natural light and create a seamless indoor-outdoor connection.
Additionally, incorporating sustainable design elements like rainwater harvesting systems and energy-efficient appliances further enhances the cost-effectiveness of concrete houses while promoting environmental consciousness.
Leveraging these design elements not only enhances the visual appeal but also contributes to creating an inviting living space that aligns with contemporary lifestyle preferences.
Long-term maintenance costs
Concrete homes have lower long-term maintenance costs compared to traditional stick-built houses. With minimal upkeep required, concrete structures are more durable and resilient against natural elements, reducing the need for frequent repairs.
This results in substantial savings over time, making concrete homes a cost-effective option for homeowners. Additionally, the energy efficiency of concrete houses contributes to long-term maintenance cost savings, as they require less heating and cooling throughout the year, further reducing overall expenses.
The durability and low maintenance requirements of concrete homes make them an attractive investment for homeowners looking to save on long-term maintenance costs while ensuring a secure and enduring living space.
Conclusion
In conclusion, building a house with concrete may entail higher initial costs. However, over time, concrete homes can offer long-term savings due to their durability and low maintenance requirements.
Despite being more expensive to build, the energy efficiency and increased resale value of concrete homes make them a cost-effective choice in the long run. Therefore, while it may not be cheaper upfront, investing in a concrete home can lead to significant financial benefits in the future.
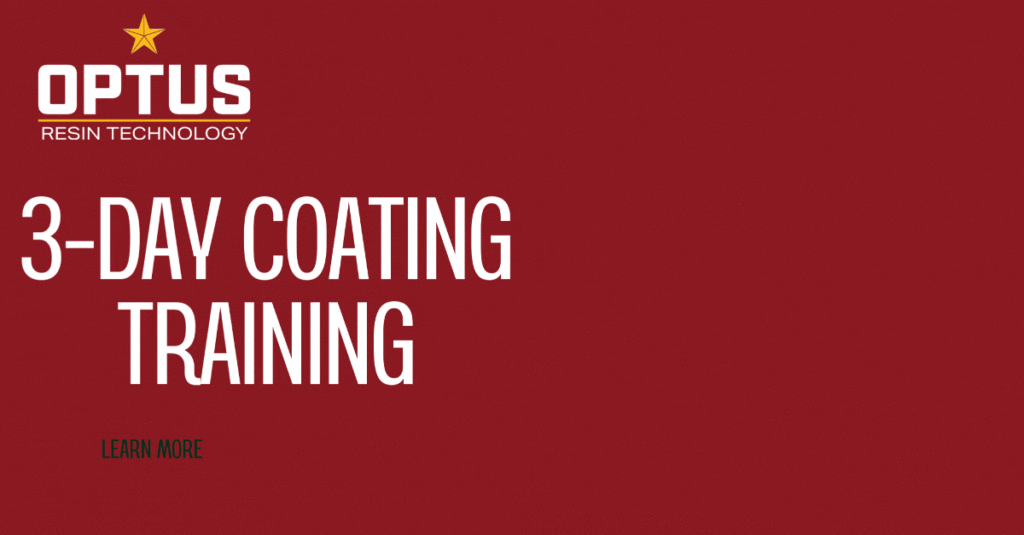
FAQs
1. Can building a house with concrete save money compared to other materials?
Yes, using ICFs or cinder block construction can often be cost-effective and cheaper than stick-built homes that use a lot of lumber.
2. Why might concrete be a more affordable option for building houses?
Concrete is considered an economical home construction material because it generally requires less maintenance over time and can provide savings on energy costs due to its insulating properties.
Recent Posts
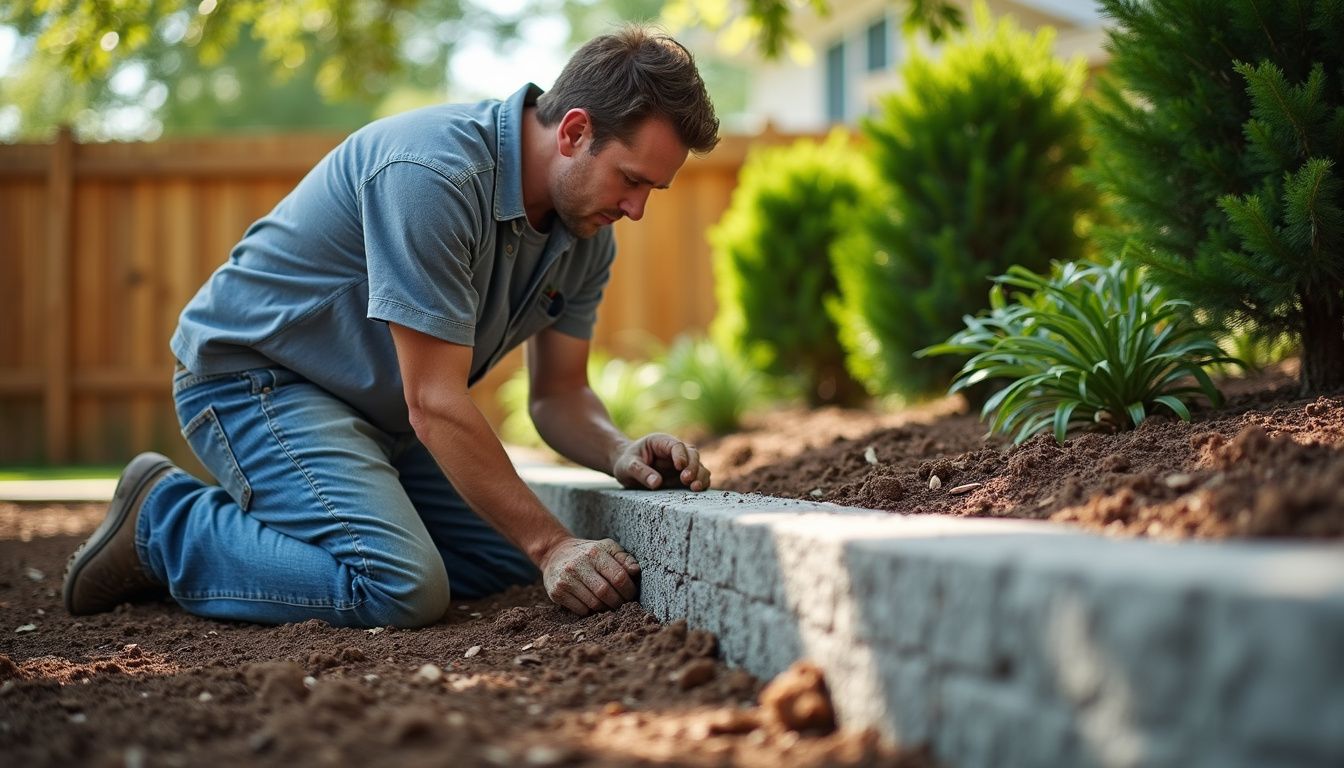
Why Landscaping Pros Prefer Precast Concrete Over Poured-in-Place
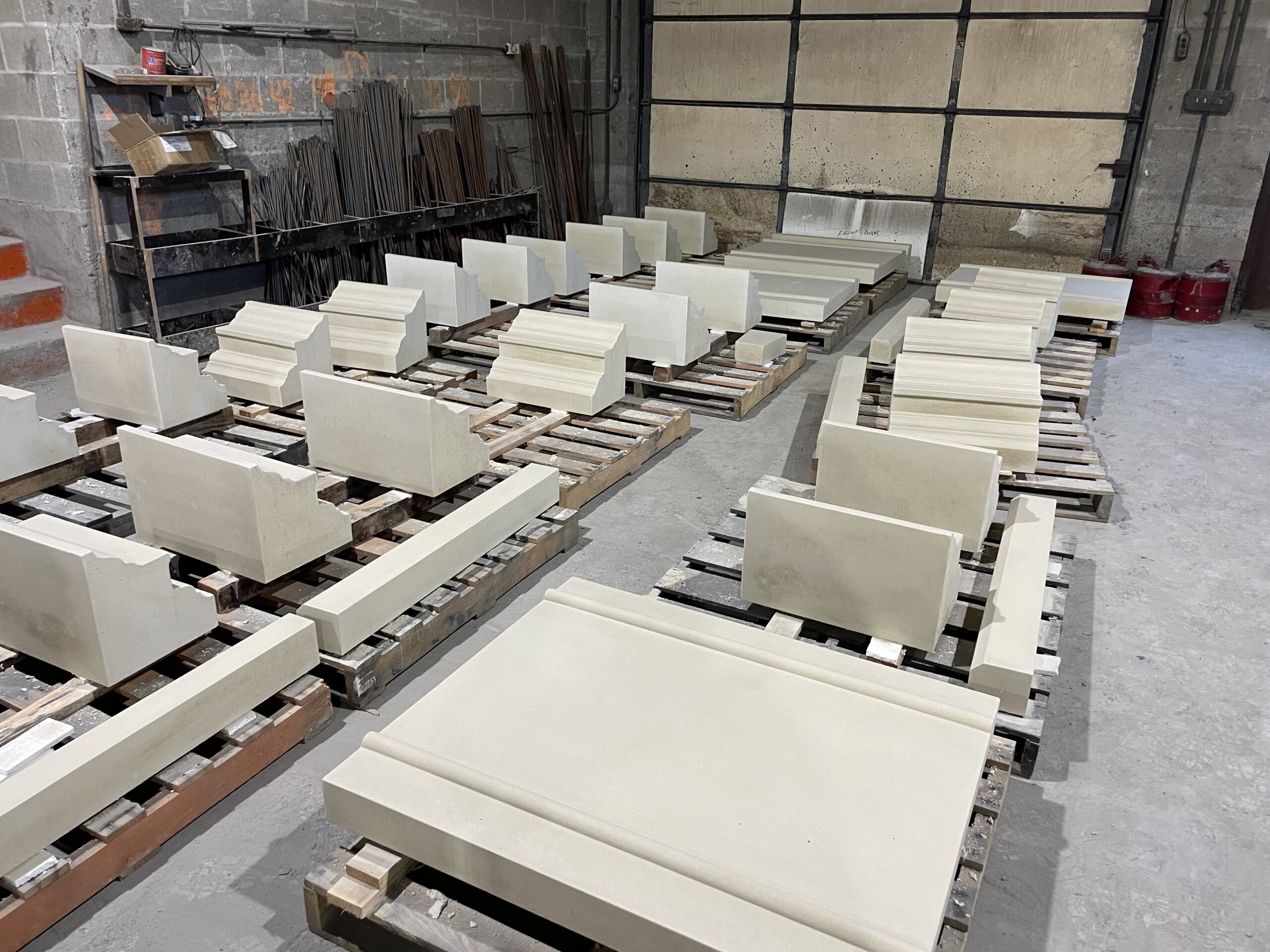
Why & How is Precast Concrete Prestressed?
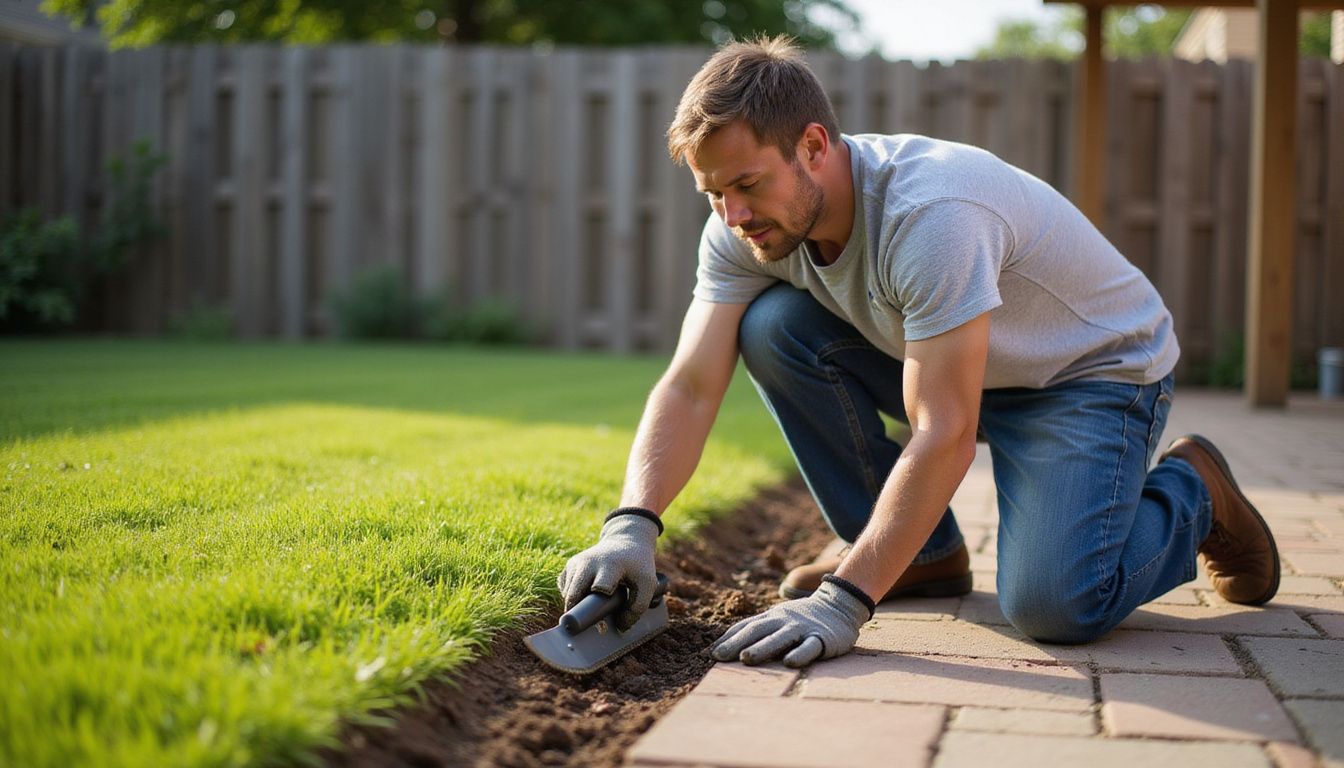