Are you wondering if the strong and durable precast concrete in buildings has rebar inside? Precast concrete often includes steel bars, known as rebar, to enhance its strength. This article will explore how rebar is used in precast concrete to make structures safer and longer-lasting.
Keep reading to discover what makes precast concrete a smart choice for construction!
Key Takeaways
- Precast concrete is often reinforced with rebar, providing extra strength and durability to withstand long-term use in building construction.
- Besides rebar, precast concrete can include welded wire fabric, pre-stressing/post-tensioning methods, or fibers for reinforcement to enhance its performance against forces and environmental conditions.
- Manufacturing precast concrete in a controlled environment leads to higher quality products with reduced risks of defects like corrosion that can compromise the structural integrity over time.
- The off – site production of precast components allows for quicker construction timelines because elements are made ahead of time and installed quickly on site.
- Fiber reinforcement in precast concrete offers an innovative solution by improving resistance to cracking and reducing maintenance needs while being more environmentally friendly compared to traditional materials.
Precast Concrete vs. Cast-in-Place Concrete
Precast concrete refers to concrete components that are molded and cured in a controlled environment before being transported and installed at the construction site, while cast-in-place concrete is poured and cured directly at the construction site.
These two methods have different reinforcement techniques and advantages in the construction industry.
Definition and differences
Precast concrete and cast-in-place concrete are two distinct methods used in the construction industry to form structural components. The main difference lies in where they are made.
Precast concrete units get their shape from molds at a factory under ideal conditions, which allows for greater quality control during the curing process. These standardized elements are then transported to the construction site ready to be installed.
Cast-in-place concrete, on the other hand, involves pouring liquid concrete into temporary or permanent molds erected at the building site. This method requires significant on-site labor and is subjected to local weather conditions that can influence its strength and durability.
Despite both methods using reinforcement technology such as steel rebar to enhance structural integrity, precast concrete ensures consistent reinforcement placement due to controlled environment manufacturing processes.
Types of Reinforcement for Precast Concrete
Precast concrete can be reinforced with rebar, welded wire fabric, pre-stressing/post-tensioning, and fiber to enhance its strength and durability. Read the full article to learn more about the different types of reinforcement for precast concrete.
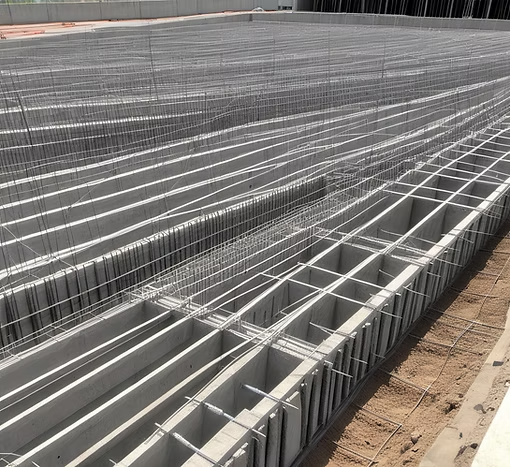
Rebar
Rebar, a steel rod used to strengthen concrete, is a vital component in precast concrete structures. It comes in various lengths and thicknesses and has been a key reinforcement technology for decades.
The design knowledge and skill required to use rebar in precast concrete are readily available, making it an accessible option for construction projects of all sizes.
Reinforced with rebar, precast structures have demonstrated their durability and strength over time. Rebar-reinforced precast concrete panels and walls are commonly used in both residential and commercial buildings due to their proven ability to enhance the structural integrity of the final construction.
Welded wire fabric
Welded wire fabric, also known as WWF or welded wire reinforcement (WWR), is a prefabricated grid specifically designed for reinforcing concrete. It consists of a series of parallel and perpendicular wires that are resistance-welded at each intersection to form a grid pattern.
Using welded wire fabric in precast concrete provides an efficient way to reinforce the material, offering strength and structural integrity. The use of welded wire fabric in precast construction helps to prevent cracking and improves durability by evenly distributing the load across the entire structure.
Builders choose welded wire fabric for its ease of handling, cutting, and placement during production. It offers versatility in reinforcing various types of precast elements such as walls, slabs, beams, and columns.
Pre-stressing/post-tensioning
Pre-stressing and post-tensioning are techniques used to reinforce precast concrete. During the pre-stressing process, steel tendons are tensioned before the concrete is poured, whereas in post-tensioning, the tendons are tensioned after the concrete has hardened.
These methods help enhance the strength and durability of precast concrete structures by placing the material under compression rather than tension. This technique significantly improves resistance against cracking and increases load-bearing capacity, making precast concrete ideal for a wide range of construction projects.
By incorporating pre-stressing or post-tensioning into precast concrete elements, engineers can minimize maintenance needs and ensure long-term structural integrity.
Fiber
As an alternative to traditional reinforcement methods like rebar and welded wire fabric, fiber is increasingly being used in precast concrete for added strength and durability. Fibers can be made from materials such as glass, steel, synthetic fibers, or natural fibers like wood.
They are mixed into the concrete before casting to enhance its tensile strength and resistance to cracking. Fiber-reinforced precast concrete offers several benefits including improved impact resistance, reduced shrinkage cracking, and increased durability against harsh environmental conditions.
Additionally, the use of fibers eliminates the need for placing and positioning traditional reinforcement materials during construction, making it a cost-effective solution.
Fiber technology in precast concrete continues to evolve with new types of fibers being developed to meet specific performance requirements. As construction moves towards sustainable practices, eco-friendly fiber options are also gaining popularity due to their low environmental impact compared to conventional reinforcing materials like steel.
Advantages of Precast Concrete
- Faster construction with precast concrete allows for quicker project completion and reduced labor costs.
- Controlled environment during precasting ensures high-quality and consistent finishes, leading to better structural integrity.
Faster construction
Precast concrete allows for faster construction compared to cast-in-place concrete. The manufacturing process takes place in a controlled environment, reducing the impact of weather and other external factors on the curing process.
With precast components being produced simultaneously with site preparation, time-saving benefits are realized as installation can begin almost immediately upon delivery.
The reduced reliance on extensive formwork and scaffolding further streamlines the construction process. Additionally, off-site production of precast elements minimizes disruption at the project site, leading to efficient assembly and shortened overall construction timelines.
This accelerated pace benefits developers seeking faster project completion without compromising quality or durability.
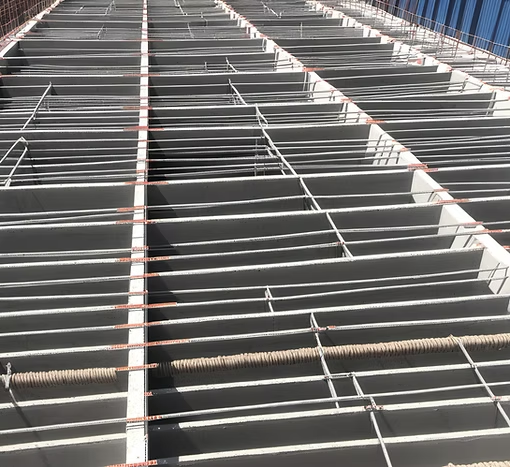
Controlled environment
The controlled environment in precast concrete manufacturing ensures consistent quality and reduces the impact of external factors on the curing process. This results in a more reliable final product that meets specific design requirements for strength and durability, crucial for reinforced concrete structures.
Additionally, by being shielded from variable weather conditions during production, precast components are less susceptible to defects caused by temperature changes or excess moisture.
In this controlled setting, the risk of corrosion to reinforcements such as rebar is significantly minimized, leading to enhanced longevity and performance of the concrete structure even in demanding environments.
Prefabricated elements are protected from environmental influences during their formative stages, allowing them to maintain their structural integrity throughout their lifespan.
Reduced risk of corrosion
With precast concrete, there is a reduced risk of corrosion compared to cast-in-place concrete. This is due to the controlled environment in which precast elements are manufactured, limiting exposure to external factors that could lead to corrosion.
Additionally, the use of high-quality materials and precise manufacturing techniques further minimizes the potential for corrosion in precast concrete structures. Innovations in concrete reinforcement technology have also contributed to enhancing the durability of precast concrete, mitigating the risk of corrosion over time.
The reduced risk of corrosion in precast concrete offers long-term benefits for construction projects by ensuring the structural integrity and longevity of the building or infrastructure.
Conclusion
In conclusion, precast concrete commonly includes rebar for reinforcement. This proven technology has been used in various construction projects and continues to evolve. The use of rebar in precast concrete provides durability and strength, making it a reliable choice for both residential and commercial buildings.
Its ease of construction, rapid production, and corrosion mitigation make it an attractive option for modern building needs. The incorporation of rebar in precast concrete underscores its importance as a durable and long-lasting construction material. Visit Vintage Cast to learn more about architectural precast concrete.
FAQs
1. Is rebar used in precast concrete?
Yes, most precast concrete includes steel reinforcement, known as rebar, to increase the strength and durability of the molded concrete.
2. Why is rebar important for precast concrete construction?
Rebar is crucial in concrete construction methods because it helps resist tension forces and supports the longevity of the structure by enhancing its overall strength.
3. How does corrosion protection work with rebar in precast concrete?
Corrosion mitigation techniques are applied during the concrete manufacturing process to protect reinforcing bars from rust that can weaken their bond with the surrounding material.
4. What happens during the concrete curing process when using precast methods?
During the curing process for precast elements, carefully controlled conditions ensure that both the reinforced bars and surrounding mixture gain maximum hardness and durability.
5. Do all types of precast concretes have steel reinforcements like rebar?
While many forms of moulded or manufactured pieces contain reinforcing bars, some smaller or non-structural designs may not require them; engineering decisions depend on intended use and required properties of finished products.
Recent Posts
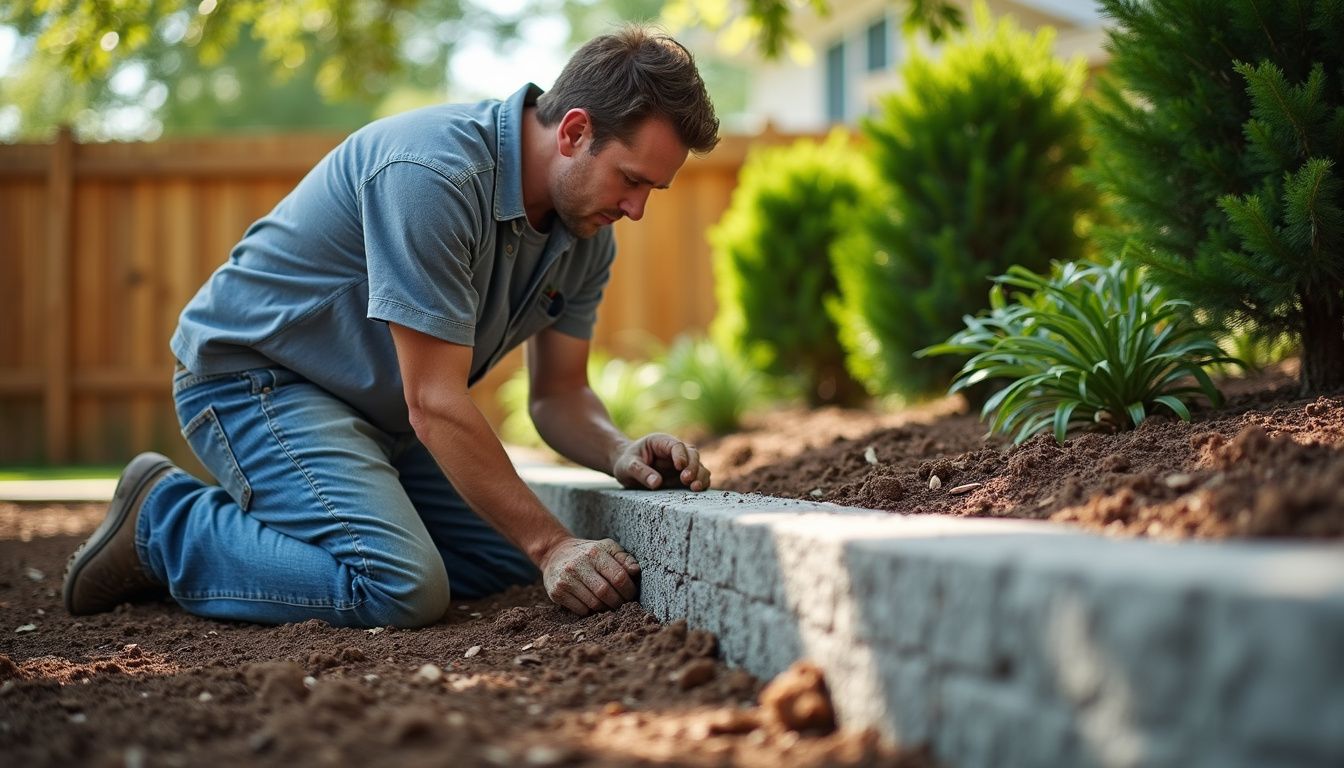
Why Landscaping Pros Prefer Precast Concrete Over Poured-in-Place
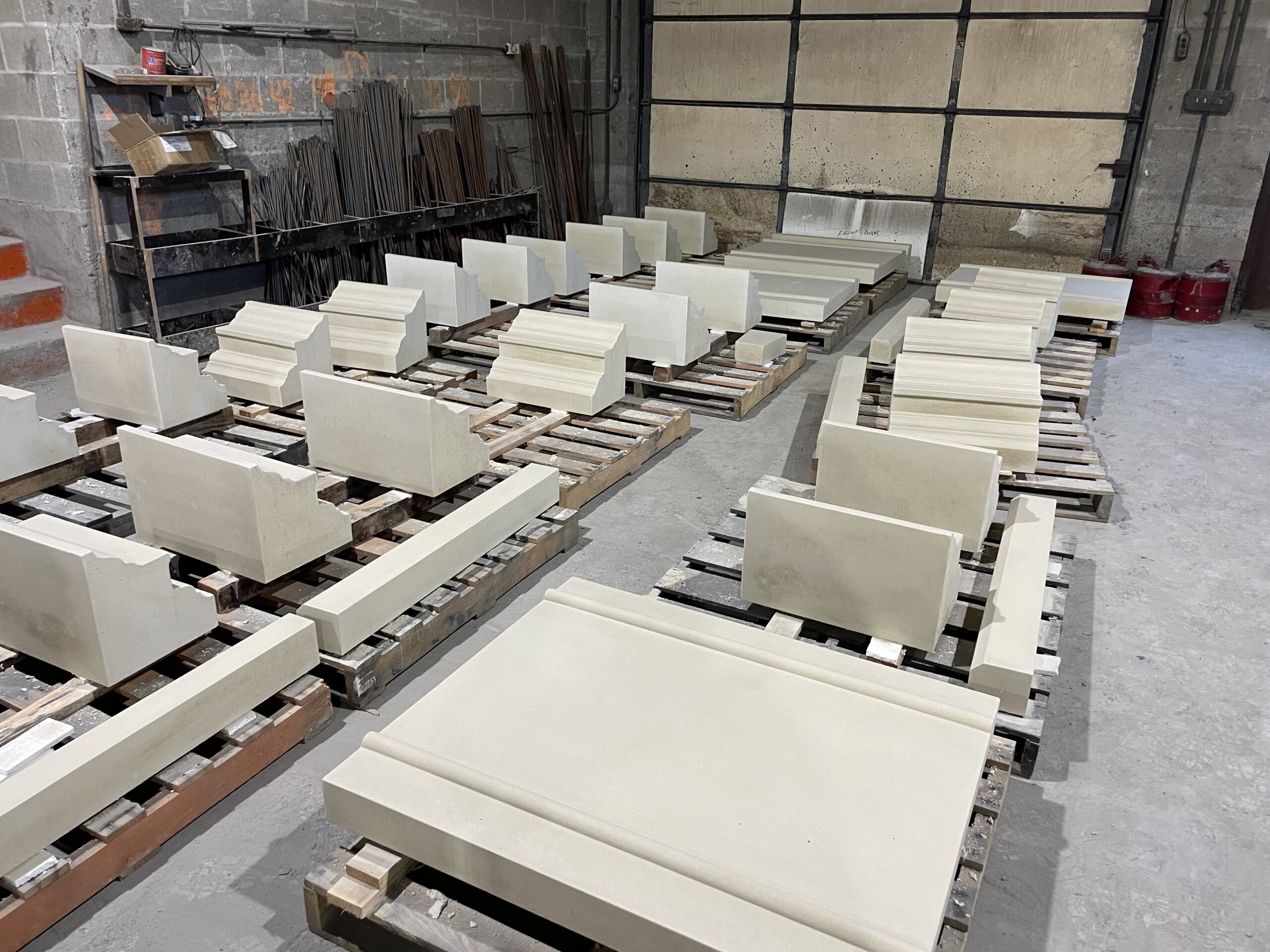
Why & How is Precast Concrete Prestressed?
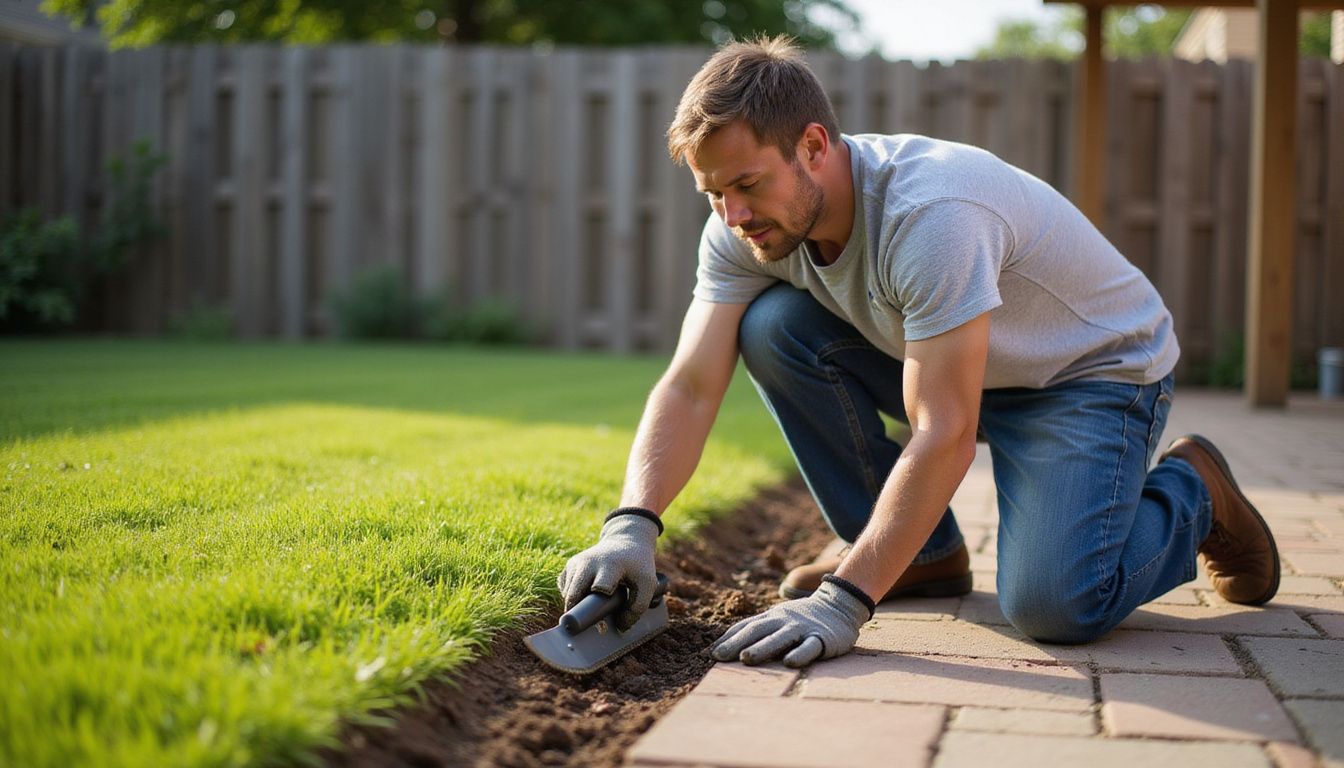