Are you noticing cracks in precast concrete and wondering if it’s normal? Concrete, while strong, is known for its tendency to develop cracks under tension. This article will explore why precast concrete cracks happen and how they can be prevented or managed effectively.
Key Takeaways
- Precast concrete can develop cracks due to tension, environmental factors like temperature and wind, as well as shrinkage during the curing process.
- Common types of precast concrete cracks include longitudinal hairline cracks, transverse cracks, diagonal cracks, random map cracking, corner cracks, and step cracks.
- Maintaining proper handling and storage conditions along with appropriate curing temperatures and moisture levels reduces the risk of cracking in precast concrete products.
- Quality control measures such as regular testing of materials and thorough inspections at every production stage are key to preventing precast concrete from cracking.
- When addressing already existing cracks in precast concrete, options like surface patching, epoxy injections, resurfacing methods or applying sealants can be used depending on the nature of the crack.
Understanding Cracks in Precast Concrete
Understanding cracks in precast concrete is important for identifying and addressing potential issues. These cracks can vary in size and type, and are caused by a variety of factors such as shrinkage, settlement, or structural loads.
What is a Crack?
A crack represents a physical split or separation in concrete, where the material has broken apart due to tension it couldn’t withstand. This breakdown might be a fine line barely visible or wider gaps that raise concerns about structural integrity.
Essentially, cracks occur when forces pull the concrete matrix and aggregates in opposite directions beyond their capacity to hold together.
Cracks show up for various reasons, including temperature fluctuations causing expansion and contraction within precast panels. The change in volume during the curing process can also lead to cracking if not managed correctly.
Concrete’s tensile properties are limited; thus, even small movements or stresses can result in cracking. Despite manufacturers’ efforts to maintain high-quality standards, some degree of cracking is inevitable due to these internal and external factors.
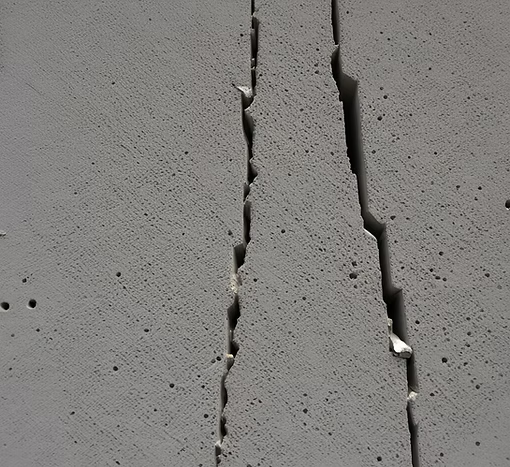
Types of Precast Cracks
Understanding the different types of cracks that can occur in precast concrete is essential for effective evaluation and maintenance. Here are the common types of precast concrete cracks:
- Longitudinal Hairline Cracks
- Transverse Cracks
- Diagonal Cracks
- Random Map Cracking
- Corner Cracks
- Step Cracks
Causes of Cracks
Causes of Cracks in Precast Concrete:
- Temperature Changes: Temperature differentials cause expansion and contraction, leading to cracks.
- Drying Shrinkage: Moisture loss during the curing process can result in concrete shrinkage and cracking.
- Wind Factors: Strong winds during curing can accelerate moisture evaporation, causing concrete to crack.
- Curing Rate: Inconsistent or rapid curing rates can lead to internal stresses and subsequent cracking.
- Heat Changes: Rapid temperature fluctuations during setting and curing can cause concrete to crack.
- Environmental Conditions: Exposure to extreme weather conditions can impact concrete integrity, resulting in cracks.
- Aggregate Issues: Poor quality or improper grading of aggregates may lead to uneven shrinkage and cracking.
Preventing Concrete Cracks in Precast Production
Proper handling, storage, and maintaining appropriate curing conditions are essential in preventing cracks in precast concrete production. Quality control measures also play a critical role in ensuring the structural integrity of precast concrete products.
Proper Handling and Storage
Handle precast concrete panels with care during transportation and storage to prevent damage that could lead to cracking.
- Ensure that all lifting inserts and anchors are properly placed and secured for safe handling and transportation of the precast panels.
- Store precast concrete panels on a flat and level surface, avoiding contact with the ground to prevent moisture absorption and potential cracking due to differential drying.
- Use appropriate lifting equipment such as slings, spreader bars, or vacuum lifters when handling precast products to avoid excessive stress that could cause cracks.
- Protect the edges and corners of precast panels during handling and storage to prevent chipping or fracturing that may lead to cracks over time.
- Implement a strict quality control process during handling and storage, ensuring that panels are not subjected to impact or mishandling that could result in structural damage or cracking.
- Monitor the environmental conditions of the storage area, keeping the temperature consistent and avoiding exposure to extreme heat or cold that may affect the integrity of the precast concrete.
Maintaining Appropriate Curing Conditions
Maintaining appropriate curing conditions is crucial to prevent cracks in precast concrete. It ensures the concrete achieves its optimal strength and durability.
- Keep the curing surface temperature consistent to avoid thermal stresses, which can lead to cracking.
- Maintain the proper humidity levels during curing to prevent rapid moisture loss, reducing the risk of shrinkage cracks.
- Use insulated blankets or thermal protection covers to regulate the curing surface temperature and minimize the impact of external environmental factors.
- Implement proper ventilation and air circulation around the curing concrete to avoid heat buildup and promote uniform drying, reducing the risk of cracking due to uneven moisture evaporation.
- Monitor and control the curing duration according to specific environmental conditions, ensuring that the concrete gains sufficient strength without experiencing excessive stress.
Quality Control Measures
To maintain the durability and strength of precast concrete, quality control measures play a crucial role. Here are some essential steps to ensure the production of high-quality precast products:
- Regular testing of concrete mix designs to verify the tensile properties and consistency in precast panel cracking.
- Implementing strict protocols for handling and storing precast concrete to prevent any damage or contamination during transportation and storage.
- Monitoring and maintaining consistent curing surface temperatures for concrete to avoid temperature differentials that can lead to cracking.
- Conducting thorough inspections at every stage of production to detect any potential issues and address them promptly.
- Ensuring proper construction techniques, including precision casting, sealing, and attention to detail, to minimize the risk of cracks in precast products.
Addressing Cracks in Precast Products
Once cracks are identified in precast products, there are cosmetic repair options available and thorough inspections are crucial to ensure the structural integrity of the product. To learn more about preventing and addressing cracks in precast concrete, read on for a detailed understanding.

Cosmetic Repair Options
When addressing cosmetic concrete cracks, there are various repair options available that can help restore the aesthetic appearance of precast products. These options include:
- Surface Patching: This involves applying a thin layer of mortar or specialized patching compound to fill in and cover small surface cracks.
- Epoxy Injection: By injecting epoxy into the cracks, it effectively bonds the adjacent concrete together, providing structural integrity and preventing further damage.
- Resurfacing: Applying a new layer of concrete or specialized resurfacing material over the existing surface to conceal cracks and provide a fresh appearance.
- Crack Stitching: Using steel or carbon fiber staples to stitch across the crack, reinforcing the concrete and preventing the crack from widening.
- Sealants: Application of specialized sealants that not only fill in cracks but also provide protection against water infiltration and environmental factors.
Importance of Thorough Inspections
To ensure the quality and durability of precast concrete products, thorough inspections are essential. Inspections help identify any cracks or defects that may compromise the structural integrity of the precast elements.
By thoroughly examining the panels, sandwich structures, or cast-in-place elements, professionals can detect hairline cracks and areas prone to damage before they worsen. This proactive approach allows for timely repairs and maintenance, contributing to the longevity and reliability of prefabricated concrete components.
Thorough inspections also aid in understanding the causes behind cracks in precast concrete. Factors such as temperature changes, drying shrinkage, curing rate, and wind impact can be evaluated through meticulous examinations.
Conclusion
In conclusion, precast concrete can crack due to various factors such as temperature changes and drying shrinkage. Preventive measures like proper handling, curing conditions, and quality control can minimize cracking.
Thorough inspections are essential for addressing any cracks that may occur in precast products. Cosmetic repair options can also help maintain the durability of precast concrete structures against cracking.
FAQs
1. Can precast concrete get cracks?
Yes, like other types of concrete, precast concrete can develop cracks due to various reasons such as changes in curing surface temperature or issues with the tensile properties of the material.
2. What causes damage to precast concrete?
Damage to precast concrete can come from things like poor bonding in the concrete matrix, excessive loads, or environmental factors that affect its durability.
3. Are there ways to stop cracks from happening in precast panels?
Preventing precast concrete cracking involves proper design and reinforcement, controlling the curing process carefully and maintaining an appropriate curing surface temperature for the concrete.
4. How does a sandwich panel help with preventing cracks?
A sandwich panel is designed to enhance durability in structures by combining layers for strength; they contribute positively towards reducing cracking risks in cast-in-place and other forms of construction.
Recent Posts
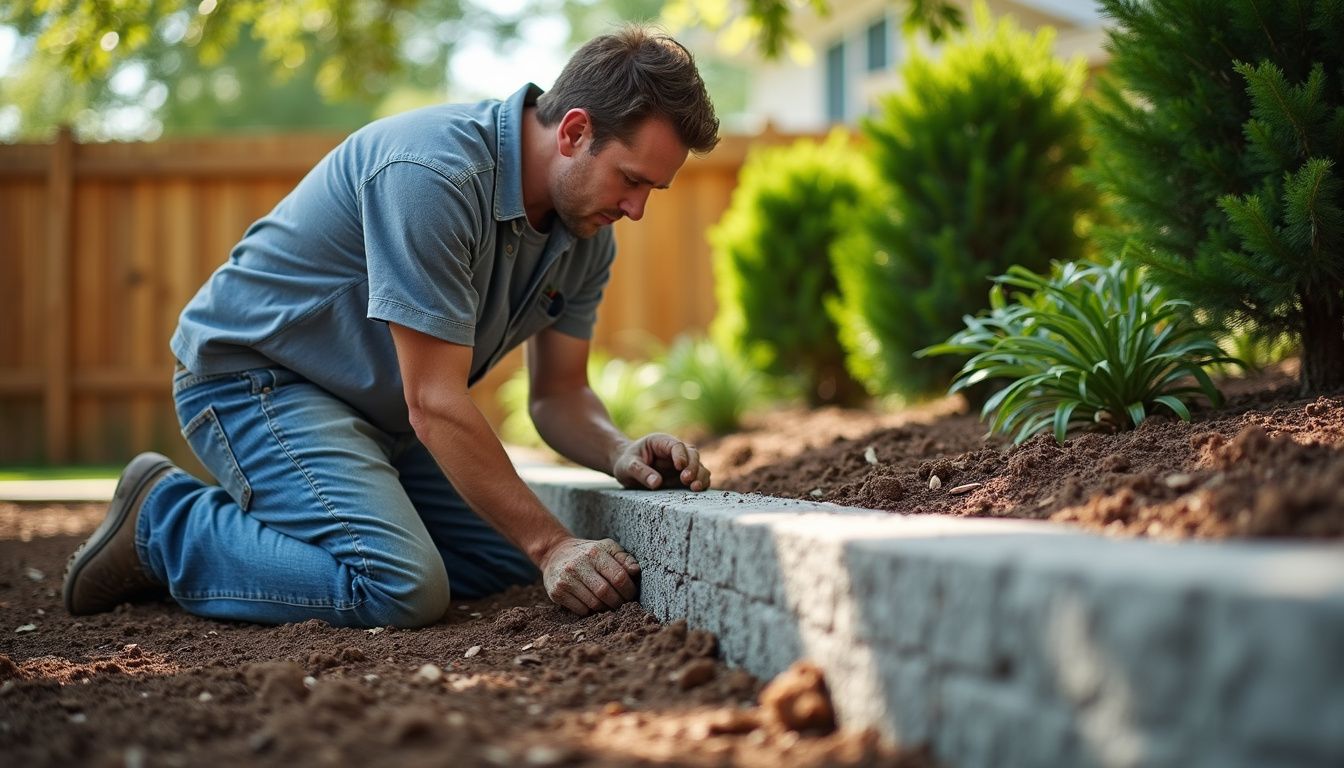
Why Landscaping Pros Prefer Precast Concrete Over Poured-in-Place
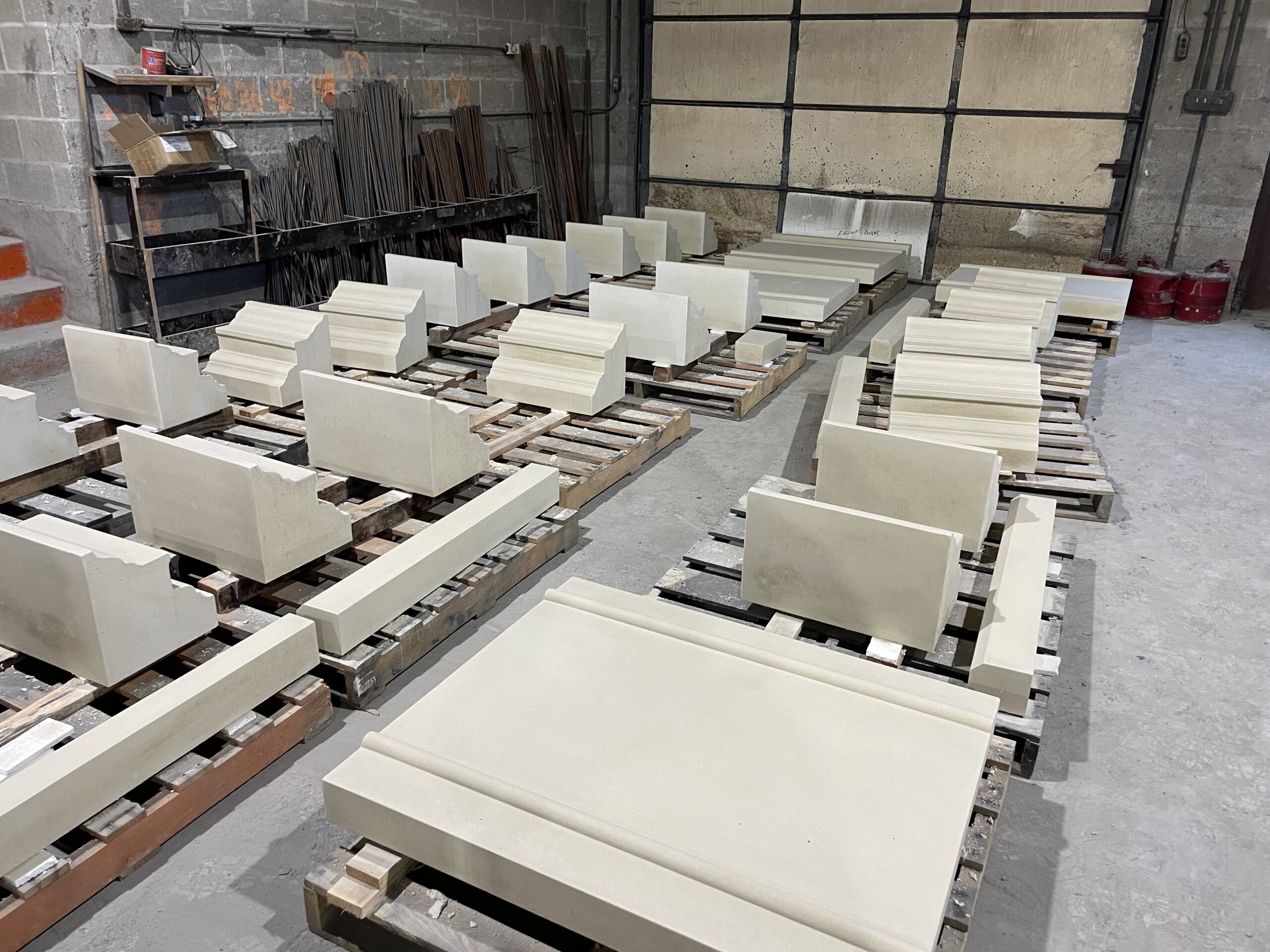
Why & How is Precast Concrete Prestressed?
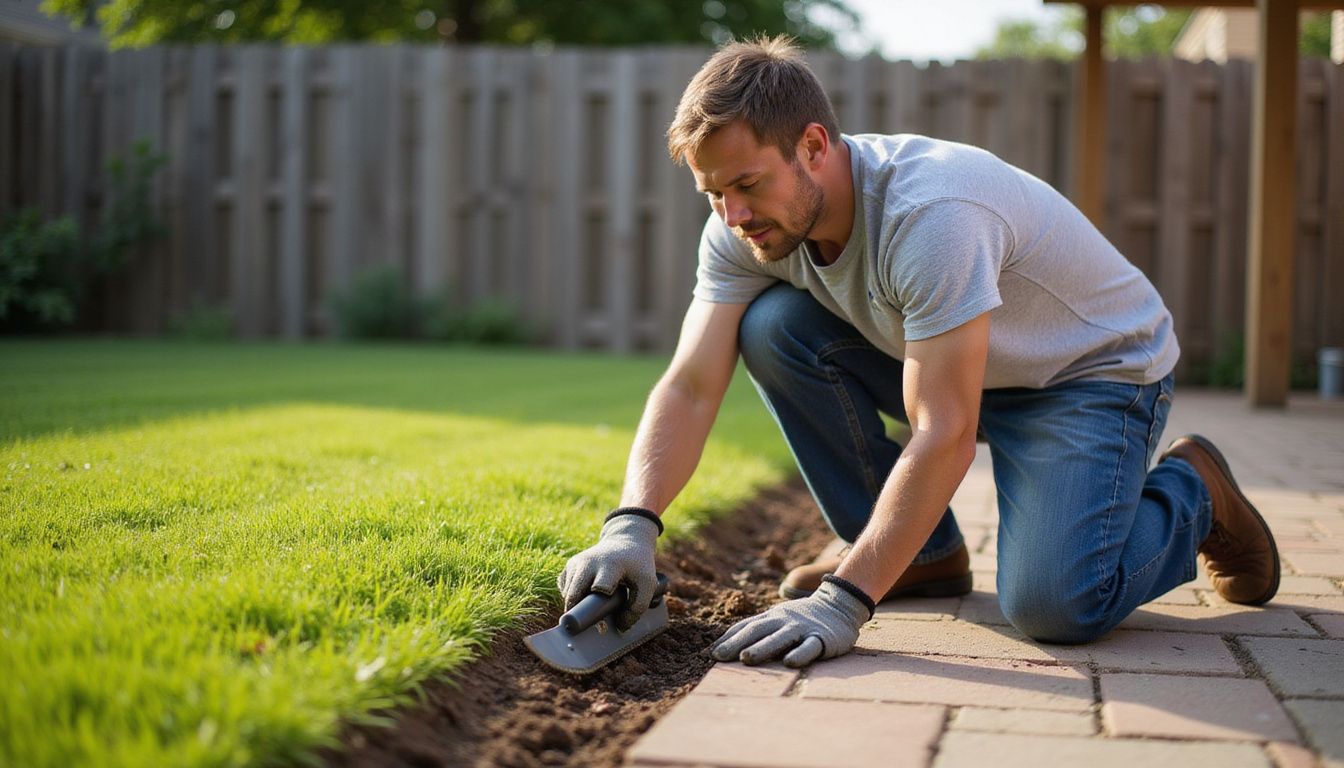